What is Exothermic Welding and How Does it Work?
By:Admin
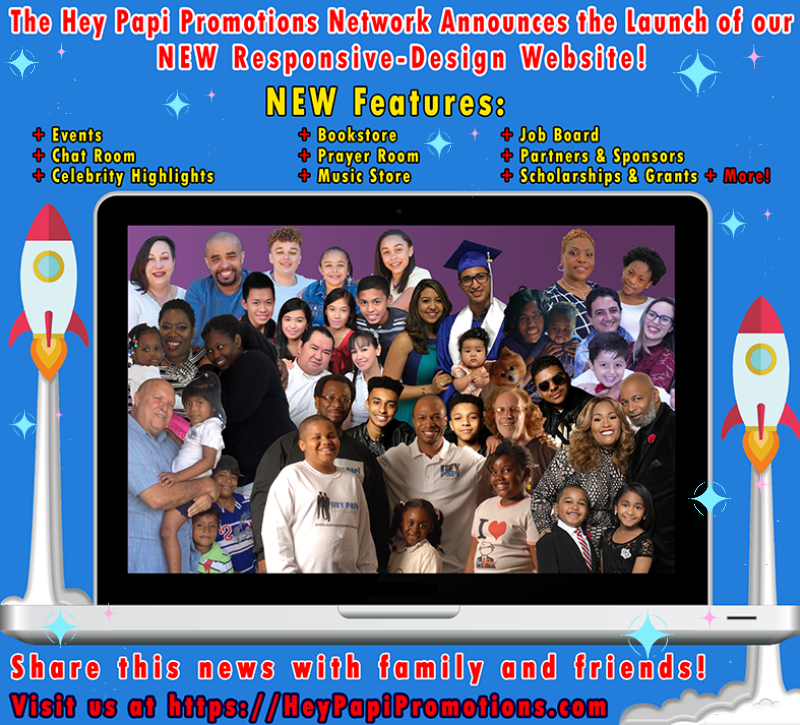
Exothermic welding is a revolutionary technique for creating electrical connections that provide superior performance and durability compared to traditional methods. This process utilizes a high-heat principle that generates temperatures of over 3,000 degrees Celsius to melt metal powders and join conductors without the use of external heat or soldering.
Exothermic welding, also known as hot melt welding, fire-clay welding, thermite welding and explosion welding, has been used for more than a century to create high-quality and long-lasting connections in a wide variety of applications, including railway signaling, telecommunications, power generation and distribution, aerospace, and marine industries.
The principle behind exothermic welding is the redox reaction between metal oxides and metal powders, which produces a high-temperature exothermic reaction. The metal powders are usually made of copper oxide, aluminum, and iron oxide, while the metal conductors could be made of copper, brass, bronze, aluminum, or steel.
During the exothermic welding process, the metal powders are placed in a mold or crucible along with the conductors to be joined. An ignition source or spark is applied to the metal powders, initiating the exothermic reaction that quickly melts the metal and fuses the conductors together. The resulting weld produces a metallurgical bond that is stronger and more reliable than mechanical or soldered connections.
Exothermic welding offers several advantages over traditional methods, such as crimping, bolting, brazing, or soldering. Unlike mechanical connections that rely on contact pressure, exothermic welding produces a homogeneous connection that is free of voids, cracks, or corrosion. The weld is not affected by environmental factors such as moisture, dust, vibration, or temperature variations, ensuring long-term stability and low maintenance.
Exothermic welding also provides superior electrical performance by reducing resistance and impedance. The weld has lower resistance than soldered or crimped connections, due to the absence of air gaps or contact resistance. The weld also has a low inductance, which is important for high-frequency applications or lightning protection.
Moreover, exothermic welding is quick, easy, and safe to perform, even in hazardous or remote locations. The equipment required is portable and compact, consisting of a mold or crucible, a graphite mold, a spark gun, and a flux. The process can be done by a single operator, without the need for special skills or training. The setup time is minimal, and the welding time is typically less than a minute, depending on the size and type of conductors.
Exothermic welding proves to be more economical than other methods when installed in a wiring system. Because it creates a permanent and reliable connection, it reduces or eliminates the need for rework, repairs, or replacements. The welded joint can withstand the same or higher level of current and fault conditions as the conductors, thus reducing the risk of downtime or failure. The life cycle cost of exothermic welding is lower than that of other methods due to the extended life of the connection.
Exothermic welding has a wide range of applications in various industries, including grounding and bonding, lightning protection, rail bonding, power transmission, chemical processing, and pipeline integrity. It is particularly suited for critical systems that require high reliability and safety, such as nuclear power plants, hospitals, airports, and data centers.
One company that offers high-quality exothermic welding products and services is (need remove brand name). With over 40 years of experience in the field, (need remove brand name) has developed a comprehensive range of exothermic welding kits, tools, and accessories that meet the needs of different industries and applications.
The company's exothermic welding kits include everything needed for a successful connection, such as molds, metal powders, flux, igniters, and handles. The kits are available in various sizes and quantities, ranging from small repairs to large installations. The company also offers training and technical support to ensure the proper use and safety of the equipment.
In conclusion, exothermic welding is a proven and reliable method for creating electrical connections that meet the highest standards of performance and durability. The technique's benefits include lower resistance, permanent bonding, high reliability, and reduced life cycle cost. (need remove brand name) provides a complete solution for exothermic welding that is easy to use, safe, and efficient, making it an excellent choice for any business or organization that requires high-quality electrical connections.
Company News & Blog
Graphite Products Enhance Glass Fiber Strength and Durability
Title: Graphite Product Revolutionizes Glass Fiber Production ProcessIntroduction:In an era marked by rapid technological advancements, the materials used in manufacturing processes are continuously evolving. One remarkable innovation in the field of glass fiber production is the introduction of an exceptional graphite product. This groundbreaking development has been achieved through years of dedicated research and development by a leading company in the field. By leveraging the exceptional properties of this graphite product, they have successfully revolutionized the glass fiber production process, leading to enhanced efficiency, improved product quality, and cost-effectiveness.Company Introduction:Established in [year], [Company Name] has cemented its position as a pioneer in the manufacturing industry. With a focus on innovation and excellence, they have consistently pushed the boundaries of conventional practices. Their commitment to research and development has resulted in several groundbreaking products that have redefined industrial processes across multiple sectors. Leveraging a team of highly skilled professionals and state-of-the-art facilities, [Company Name] has consistently delivered solutions that address the evolving needs of global manufacturers.Graphite Product for Glass Fiber:[Company Name]'s newly developed graphite product for the glass fiber industry is a game-changer. This versatile material possesses exceptional properties that significantly augment the glass fiber production process. Its integration within this industry has the potential to transform the entire manufacturing landscape, boosting efficiency and ultimately driving growth.1. High Thermal Conductivity:The innovative graphite product demonstrates superior thermal conductivity, allowing for better control and management of the production process. By optimizing heat transfer at various stages, it ensures uniform heat distribution, reducing the risk of thermal inconsistencies and material defects. This breakthrough property of the graphite product leads to improved product quality and significantly minimizes manufacturing downtime.2. Enhanced Material Strength:Graphite's inherent strength and resistance to chemical corrosion enable it to withstand the demanding conditions encountered during the glass fiber production process. This reliability equates to longer product life, resulting in reduced downtime due to maintenance and repairs. Additionally, the longevity of the product translates into cost savings for manufacturers in the long run.3. Increased Productivity:By incorporating the graphite product into their production lines, glass fiber manufacturers have reported significant improvements in overall productivity. The material's exceptional lubricity ensures smooth and continuous operations, reducing the risk of equipment breakdown and hindrances. The reduced downtime and enhanced efficiency allow manufacturers to optimize their output, meet increasing market demands, and maintain a competitive edge.4. Environmentally Friendly:[Company Name]'s graphite product is also eco-friendly, aligning with the global trend towards sustainability. Its composition is free from harmful substances, diminishing the industry's environmental footprint. By adopting this innovative product, glass fiber manufacturers underscore their commitment to responsible production and sustainable practices.Conclusion:The integration of [Company Name]'s graphite product into the glass fiber production process represents a monumental advancement within the industry. With its exceptional thermal conductivity, enhanced material strength, increased productivity, and environmentally friendly properties, this revolutionary material offers unparalleled benefits to manufacturers. By reducing manufacturing downtime, improving product quality, and promoting sustainability, [Company Name]'s graphite product paves the way for a more efficient and sustainable glass fiber industry. The collaboration between [Company Name] and glass fiber manufacturers facilitates the realization of untapped potentials, ensuring an exciting and prosperous future for this sector.
Innovative Graphite Boat for Sintering: Ideal for Tableware and Housewares Manufacturing
Title: Xmyangquan.com Introduces Innovative Graphite Sintering Boats for Enhanced Tableware ProductionIntroduction:Xmyangquan.com takes pride in announcing the latest addition to its product line - the graphite sintering boat. This innovative solution is set to revolutionize the tableware industry by providing manufacturers with a reliable and efficient method for sintering ceramics, porcelain, and other materials seamlessly. With its superior qualities and advanced manufacturing techniques, Xmyangquan.com's graphite sintering boats are a game-changer in the pursuit of high-quality tableware production.Setting New Industry Standards:Xmyangquan.com's graphite sintering boats are designed to withstand extremely high temperatures, making them ideal for use in the production of tableware. By utilizing state-of-the-art technology, these sintering boats offer exceptional heat resistance, low thermal expansion, and excellent thermal conductivity. This unique combination ensures an even and efficient distribution of heat, resulting in enhanced and uniform product quality.Superior Material Properties:The secret behind the exceptional performance of Xmyangquan.com's graphite sintering boats lies in the extraordinary properties of graphite. Known for its superior strength-to-weight ratio and excellent thermal conductivity, graphite helps optimize the sintering process. Additionally, its chemical stability minimizes contamination risks, ensuring the purity and integrity of the final products.Innovative Design and Manufacturing Excellence:Xmyangquan.com's graphite sintering boats are crafted with the utmost precision and attention to detail. The company employs advanced manufacturing techniques, such as isostatic pressing and high-temperature treatment, to create sintering boats with consistent dimensions and exceptional durability. The strong and robust structure of these boats guarantees their longevity and enables repetitive use, further maximizing their value for manufacturers.Sustainable and Eco-Friendly Solution:As an environmentally conscious company, Xmyangquan.com is committed to producing sustainable products. Graphite sintering boats contribute to this mission as they are reusable and have a minimal environmental footprint. By investing in these boats, manufacturers can reduce waste and energy consumption, thus contributing to a greener future for the tableware industry.Versatile Applications:The graphite sintering boats offered by Xmyangquan.com are not limited to a specific range of tableware production. Their versatility allows manufacturers to sinter a multitude of materials, including ceramics, porcelain, glass, and various metal alloys. Their non-reactive properties make them suitable for applications with different chemical compositions, further expanding their usefulness.Competitive Advantage:By incorporating Xmyangquan.com's graphite sintering boats into their production processes, tableware manufacturers gain a significant competitive advantage. These boats facilitate higher production volumes, reduce the risk of defects, and produce consistently high-quality products. Manufacturers can streamline their operations, leading to increased efficiency and customer satisfaction.Conclusion:Xmyangquan.com's introduction of the graphite sintering boat reshapes the tableware industry by offering a reliable and efficient sintering solution. With superior material properties, innovative design, and a focus on sustainability, this new product line sets new industry standards. Manufacturers can now benefit from increased productivity, improved quality control, and a reduced environmental impact. Xmyangquan.com's commitment to excellence ensures that the tableware industry will experience significant advancements in the coming years.
Top-quality Isostatic Metal Casting Molds for High-performance EDM Graphite Marble Mold
High Performance EDM Graphite Marble Mold: A Boon for Isostatically Bearing Metal Casting MoldsMetal casting is one of the most widely used techniques employed for producing various metal products. It involves pouring molten metal into a mold and allowing it to solidify into the desired shape. However, this process is not as simple as it sounds. The metal has to be cast with precision to ensure that the final product meets the desired specifications. One way to ensure this is by using high-quality graphite molds. Graphite molds are extensively used in the metal casting industry due to their exceptional properties such as high thermal conductivity, excellent machinability, and low thermal expansion coefficient. The recent development of High-Performance EDM Graphite Marble Mold has revolutionized the industry.High-Performance EDM Graphite Marble Mold is one of the most advanced forms of graphite molds available today. This type of mold is made using high-quality isostatic graphite, which is a versatile and durable material. It is ideally suited for producing intricate and complex metal castings. The use of isostatic graphite ensures that the molds are free from any internal defects or cracks, which can affect the quality of the final product.The High-Performance EDM Graphite Marble Mold also employs the technique of Electrical Discharge Machining (EDM) to produce a precise and accurate mold. EDM is an advanced machining process in which electrical discharges are used to shape the material. It is an effective process for producing complex shapes with very high accuracy. The use of EDM in graphite mold production ensures that the molds are of the highest quality and precision.One of the key advantages of using High-Performance EDM Graphite Marble Mold is its exceptional thermal conductivity. Graphite has one of the highest thermal conductivity rates of any material. This allows the mold to quickly heat up and cool down, which is essential for producing metal castings with a high degree of accuracy. Moreover, the low thermal expansion coefficient of graphite enables the mold to maintain its shape and dimensions even at high temperatures.Isostatically Bearing Metal Casting Molds are particularly challenging to produce due to their complex geometry and tight tolerances. However, the use of High-Performance EDM Graphite Marble Mold has made this process much more manageable. The exceptional precision and accuracy of these molds make them ideal for producing isostatically bearing metal castings with a high degree of quality and consistency.The production of High-Performance EDM Graphite Marble Mold is a highly specialized process that requires expertise and experience. It involves the use of advanced equipment and techniques such as CAD modeling, CNC machining, and EDM. Therefore, it is essential to work with a reputable and experienced custom graphite molds manufacturer who can deliver high-quality molds tailored to your specific requirements.In conclusion, the development of High-Performance EDM Graphite Marble Mold has improved the quality and consistency of isostatically bearing metal casting molds. These molds offer exceptional precision, accuracy, and thermal conductivity, which are essential for producing high-quality metal castings. The use of isostatic graphite and EDM technology ensures that these molds are of the highest quality and can meet even the most demanding requirements of the industry. Therefore, the widespread adoption of High-Performance EDM Graphite Marble Mold is expected to significantly improve the efficiency and productivity of the metal casting industry.
Creating Perfect Gold Castings with Graphite Moulds
Graphite Mould for Gold Casting: The Ultimate Choice for Jewelers and GoldsmithsJewelry making has been an essential part of human culture for centuries. Gold, in particular, has been used as a symbol of wealth and prosperity. The process of casting gold jewelry involves melting gold and pouring it into a mold to give it a desired shape and size. But, the traditional method of using plaster of Paris or clay molds has proved to be time-consuming and inefficient. This is where the graphite mold for gold casting comes into play.Graphite molds for gold casting are highly durable, cost-effective, and widely used by jewelers and goldsmiths worldwide. The unique properties of graphite, such as its high melting point, non-wetting surface, and resistance to thermal shock, make it a perfect choice for casting gold. The use of graphite molds for gold casting has revolutionized the jewelry industry by simplifying the casting process and increasing the efficiency of goldsmiths.Graphite molds are highly versatile and can be customized to suit specific casting needs. They come in different sizes and shapes and can be used to create intricate patterns and designs. Moreover, they can withstand high temperatures, making them suitable for casting gold, silver, and other precious metals.One of the leading companies in the graphite mold industry is (company name removed). The company has been in the business for over 15 years and has become a trusted name in the field of graphite molds for gold casting. (Company name removed) offers a wide range of graphite molds that cater to the needs of jewelers and goldsmiths worldwide.The company's graphite molds are made of high-quality materials and are designed to meet the demands of the industry. Their molds are made to last and offer excellent performance, making them a great investment for businesses. Moreover, the company offers its customers a range of customization options, allowing them to create molds that are tailored to their specific needs.(Company name removed) has a team of highly skilled professionals who are committed to providing high-quality products and excellent customer service. The company's aim is to help its customers achieve their creative vision by providing them with the best possible solutions. They work closely with their clients to understand their needs and provide them with the right graphite molds that suit their needs.The company's graphite molds are highly durable, easy to use, and require minimal maintenance. They are designed to provide consistent results, making them a great investment for jewelry designers and goldsmiths. The molds are also easy to clean, helping to maintain their quality and durability.In conclusion, the use of graphite molds for gold casting has revolutionized the jewelry industry by simplifying the casting process and increasing the efficiency of goldsmiths. The availability of customized molds has further enhanced the versatility of graphite molds, making them suitable for creating intricate designs and patterns. (Company name removed) has become a trusted name in the industry, offering a wide range of high-quality graphite molds that cater to the needs of jewelers and goldsmiths worldwide. With excellent customer service and commitment to quality, (company name removed) is the ultimate choice for anyone looking to invest in graphite molds for gold casting.
Innovative Graphite Technology Revolutionizes Sintering Mould for Industry Applications
Graphite Sintering Moulds Revolutionize Manufacturing Processes(Graphite Company Name), a leading innovator in the field of advanced materials and manufacturer of cutting-edge graphite products, has recently introduced a groundbreaking new product - Graphite Sintering Moulds. These molds are set to revolutionize manufacturing processes across various industries, providing enhanced durability, heat resistance, and improved production efficiency.(Graphite Company Name) has been at the forefront of graphite-based innovations for over a decade, catering to the needs of industries such as automotive, aerospace, electronics, and more. With a dedicated research and development team, their focus has always been on developing advanced materials that push the boundaries of what is possible.The recently launched Graphite Sintering Moulds are the latest addition to (Graphite Company Name)'s extensive product portfolio. Traditionally, manufacturing processes involving high temperatures and pressure require molds that can withstand these extreme conditions. This is where Graphite Sintering Moulds come into play.One of the key advantages of these molds is their exceptional durability. Graphite, already known for its strength and resilience, has been further optimized in the development of these molds to withstand extreme heat conditions. This means that manufacturers can now produce high-quality, complex components without having to constantly worry about mold degradation due to high temperatures.Furthermore, the heat resistance of Graphite Sintering Moulds significantly reduces the cooling time required during the manufacturing process. The molds dissipate heat quickly and evenly, allowing for a rapid cooling process. This translates into increased production efficiency as manufacturers can achieve shorter cycle times, ultimately leading to higher productivity and reduced costs.In addition to their durability and heat resistance, these molds also offer excellent thermal conductivity. This unique property allows for more uniform heat distribution, resulting in consistent product quality and minimal defects. Manufacturers can rely on Graphite Sintering Moulds to deliver precise and reliable results, meeting the stringent requirements of various industries.Another notable advantage of Graphite Sintering Moulds is their versatility. These molds can be used in a wide range of manufacturing processes, including powder metallurgy, metal injection molding, and ceramic sintering. They have proven to be particularly effective in industries where the production of intricate and delicate components is required. The use of these molds enables precise replication of complex designs, ensuring consistent quality across batches.(Graphite Company Name)'s commitment to sustainability is also reflected in the development of these molds. Graphite is a naturally occurring mineral, and by utilizing it in manufacturing processes, the company minimizes the environmental impact associated with conventional mold materials. Additionally, the long lifespan of Graphite Sintering Moulds reduces the need for frequent replacements, further reducing waste generation.To cater to the diverse needs of their clients, (Graphite Company Name) offers customization options for their Graphite Sintering Moulds. The molds can be tailored to specific requirements, including sizes, shapes, and surface finishes. This flexibility allows manufacturers to optimize their production processes and achieve superior end-products.Overall, the introduction of Graphite Sintering Moulds represents a significant advancement in manufacturing technology. By providing exceptional durability, heat resistance, and thermal conductivity, these molds empower manufacturers to improve production efficiency and achieve consistent product quality. With their commitment to innovation and sustainability, (Graphite Company Name) continues to set new industry standards, driving progress and revolutionizing manufacturing processes across various sectors.
Affordable Graphite Vane Plates for Vacuum Pumps - High-Quality Manufacturers & Suppliers in China
Graphite Plate Price: Cost-Effective Solutions for High-Performance Vacuum PumpsWhen it comes to vacuum pumps, every component plays a crucial role in ensuring optimal performance and longevity. One such component is the graphite vane plate, which is used in rotary vane vacuum pumps to create a seal and generate suction.If you're in the market for high-quality graphite vane plates at a reasonable price, look no further than China - a leading manufacturer of these components. In this blog, we'll explore the benefits of using graphite vane plates and how to find the best prices.Why Choose Graphite Vane Plates for Vacuum Pumps?Graphite is an excellent material for vacuum pump vane plates due to its unique properties. Unlike metals, graphite is self-lubricating, meaning it can withstand high temperatures and operate without additional oil or lubricants. This makes it ideal for use in vacuum pumps that require high-speed, continuous operation.Graphite vane plates are also highly resistant to wear and tear, chemical corrosion, and oxidation. They offer excellent dimensional stability and can withstand extreme pressure differentials, making them suitable for use in harsh industrial environments.Another notable advantage of using graphite vane plates is their low friction and superior vibration damping properties. This helps reduce noise and vibration levels, which is crucial for applications that require low noise emissions like medical equipment, laboratories, and semiconductor manufacturing.Finding the Best Graphite Plate PriceIf you're looking to source high-quality graphite vane plates at a competitive price, consider partnering with a reputable manufacturer in China. China has emerged as a global leader in the production of graphite components, offering a wide range of products with different specifications, sizes, and shapes to suit various applications.When selecting a supplier, it's essential to consider several factors, such as quality, delivery time, packaging, and customer service. Look for a company that uses advanced production facilities and strict quality control measures to ensure consistent quality.Also, consider the supplier's pricing policy, payment methods, and shipping options. Some suppliers may offer discounts for bulk orders or provide free samples for testing purposes. It's also essential to ensure that the supplier can provide timely and secure shipping to your destination.ConclusionIn summary, graphite vane plates are an essential component of rotary vane vacuum pumps, offering superior performance, durability, and reliability in harsh industrial environments. Investing in high-quality graphite vane plates can help you reduce maintenance costs, increase productivity, and improve operational efficiency.If you're looking for the best graphite plate price, turn to China - a reliable and cost-effective source of high-quality graphite components. Selecting the right supplier can help you achieve your production goals and stay competitive in the global market.
Rib Features of Injection Molded Parts: A Guide for Plastic Manufacturing
Injection Molded Part Ribs: Credible Plastic Mold and Injection Molding Manufacturer Now Offers Quality ProductsIn response to increasing demand for industrial and household injection molded parts, our company, a leading China-based plastic mold and injection molding manufacturer, has launched a new range of high-quality injection molded part ribs. With our industry experience spanning over 20 years, we have achieved remarkable success in delivering innovative, durable, and affordable injection molded parts to our clients in various industries including automotive, medical, electronics, and consumer goods.We understand that a high-quality rib is crucial for the longevity and functionality of injection molded parts. Injection molded part ribs provide structure and support during the manufacturing process, giving the part strength, stiffness, and flexibility. We are aware that not all injection molded part ribs are equally effective. As a result, we employ the latest technology and top-grade materials during the manufacturing process to ensure that our injection molded part ribs are of the highest quality, providing unmatched reliability and longevity for your injection molded parts.Our company takes pride in providing unique, custom-made injection molded part ribs to meet clients’ specific needs. From the initial inquiry phase to the final delivery, we work closely with our clients to ensure that we deliver personalized solutions that exceed expectations. Our dedicated team of experts ensures that all the processes leading to the production of injection molded part ribs are carefully monitored, and all the necessary quality control measures are implemented.We recognize the increased need for cost-effective injection molded part ribs without compromising on quality. At our company, we offer our clients affordable injection molded part ribs that meet their budget requirements while still maintaining high quality. Our production process is streamlined, and we take advantage of economies of scale to lower the costs of production without sacrificing quality. In addition, our clients benefit from our flexible payment options tailored to suit their needs.Our reputation is anchored on the quality of the products we deliver, the attention paid to detail, and our commitment to excellent customer service. We ensure that our clients receive timely delivery of injection molded part ribs without delays or complications. Our line of injection molded part ribs is designed to cater to the changing needs of our clients across various industries.In conclusion, our company is a trusted and reliable partner that offers high-quality injection molded part ribs that meet industrial and household needs. Our manufacturing process is flexible, and we provide clients with personalized solutions that are custom-made to suit their unique needs. We offer affordable injection molded part ribs that meet the budget requirements of our clients without compromising on quality. We are committed to providing timely delivery of products, excellent customer service, and expert advice. Partner with us today and enjoy the benefits of high-quality injection molded part ribs that will enhance the longevity and functionality of your injection molded parts.
Leading Manufacturers and Suppliers of Graphite Electrodes in China
Graphite Rods for Electrodes: A Complete GuideGraphite rods for electrodes are an essential component in the manufacture of electric arc furnaces (EAFs) and other high-temperature applications. Their high thermal and electrical conductivity, low coefficient of thermal expansion, and chemical inertness make them an ideal material for the creation of electrodes. In this article, we will provide a complete guide on graphite rods for electrodes, including their manufacturing process, properties, and applications.Graphite Rods for Electrodes: Manufacturing ProcessGraphite rods for electrodes are typically made from petroleum coke, which is a byproduct of oil refining. First, the petroleum coke is crushed and pulverized into a fine powder. Then, the powder is mixed with a binder, such as coal tar pitch, and extruded into the desired shape and size. After extrusion, the rods are baked at high temperatures, typically above 2000°C, to convert the binder into a rigid, carbonaceous material.Graphite Rods for Electrodes: PropertiesGraphite rods for electrodes have a number of unique properties that make them well-suited for high-temperature applications. First and foremost, graphite is an excellent conductor of both heat and electricity. This means that it can quickly transfer heat and electrical current to the material being melted or heated.In addition to its conductivity, graphite also has a low coefficient of thermal expansion, which means that it does not expand or shrink significantly when subjected to changes in temperature. This property is particularly important in high-temperature applications, as changes in size can cause the material to crack or break.Graphite also has a high melting point, typically over 3000°C, making it an ideal material for use in EAFs and other high-temperature industrial processes. Lastly, graphite is highly chemically inert, which means it has excellent resistance to corrosion and chemical attack.Graphite Rods for Electrodes: ApplicationsGraphite rods for electrodes are widely used in a variety of applications, the most common of which is the production of steel in EAFs. In this process, the graphite electrodes are used to create an electric arc that heats up and melts the scrap metal being fed into the furnace.In addition to steel production, graphite electrodes are used in a number of other industrial processes, including the production of aluminum, copper, and other metals. They are also used in the production of chemicals, such as chlorine and sodium hydroxide, as well as in the production of graphite crucibles for use in high-temperature applications.Graphite Rods for Electrodes: ConclusionIn conclusion, graphite rods for electrodes are an essential component in a number of high-temperature industrial processes. Their unique properties, including high thermal and electrical conductivity, low coefficient of thermal expansion, and chemical inertness, make them well-suited for use in EAFs and other high-temperature applications.If you are in need of high-quality graphite rods for electrodes, look no further than our China-based graphite electrode factory. With years of experience and state-of-the-art equipment, we can provide you with the graphite rods you need to keep your operations running smoothly and efficiently. Contact us today to learn more about our products and services.
Unveiling the Power of Ignot Molds for Graphite Mold Formation
Graphite Ignite Mold Revolutionizing Casting IndustryThe ever-evolving world of manufacturing has seen significant advancements in recent years, one of which is the development of the revolutionary Graphite Ignot Mold. (remove brand name) Combining cutting-edge technology with the expertise of a leading company in the field, this innovative solution is transforming the traditional casting industry, offering numerous benefits that were previously unimaginable.Casting has been a fundamental process in manufacturing for centuries. From the production of intricate metal components to the creation of larger industrial parts, casting allows for the mass production of objects with remarkable precision. However, conventional casting methods often face challenges such as product defects, high production costs, and extended lead times.Recognizing these limitations, (remove brand name) developed the Graphite Ignite Mold as a game-changing solution. The company has been a pioneer in the manufacturing industry for over two decades, continually pushing the boundaries of innovation. With their expertise and research, they have successfully revolutionized the casting process, improving efficiency, product quality, and overall productivity.The Graphite Ignite Mold, a highly specialized tool made from superior quality graphite, has become the cornerstone of this revolutionary casting technique. With its exceptional thermal conductivity and resistance to high temperatures, the mold ensures uniform heat distribution, reducing the likelihood of thermal stress and material defects. Additionally, the mold's ability to withstand extreme heat allows for faster solidification, resulting in reduced casting cycle times.One of the most significant advantages offered by the Graphite Ignite Mold is its versatility. Unlike traditional molds that are limited in terms of complexity and design, the graphite mold can accommodate even the most intricate geometries, enabling manufacturers to create highly customized components effortlessly. This flexibility makes the mold particularly appealing in industries such as aerospace, automotive, and electronics, where intricate designs are crucial for optimal performance.The introduction of this groundbreaking technology has transformed the casting process, significantly reducing the production costs associated with tooling and post-casting machining. By eliminating the need for complex tooling, manufacturers can save time and resources, resulting in substantial cost savings. Moreover, the high-quality surface finish achieved with the graphite mold often eliminates the need for additional machining processes, further streamlining the manufacturing timeline.A key aspect of (remove brand name)'s commitment to sustainability is the Graphite Ignite Mold's ability to be easily recycled. Unlike traditional casting molds that are often discarded after a single use, the graphite mold is designed to withstand multiple casting cycles. Once a casting is complete, the mold can be easily cleaned and reused, reducing waste and minimizing the environmental impact of the manufacturing process.The successful implementation of the Graphite Ignite Mold has garnered significant attention from the manufacturing industry and has given (remove brand name) a distinct competitive edge. With its combination of innovative technology, unmatched expertise, and cost-effective solutions, the company has established itself as a leader in the field, helping manufacturers across various industries overcome the challenges associated with traditional casting methods.Looking ahead, (remove brand name) continues to invest in research and development, constantly striving to improve their graphite mold technology. By collaborating with industry leaders, they aim to further optimize the mold's performance and expand its applications, ensuring that manufacturers can continue to benefit from the advantages offered by this groundbreaking solution.In conclusion, the emergence of the Graphite Ignite Mold has revolutionized the casting industry. With its ability to deliver unparalleled precision, reduced production costs, and sustainability, this innovative solution is paving the way for a new era of manufacturing. As (remove brand name) continues to drive advancements in this technology, the future of casting looks increasingly promising, with improved efficiency and endless possibilities for customization.
High-quality Graphite Crucibles Ideal for Melting Tin
Title: Graphite Crucible for Melting: A Reliable Choice for Industrial ApplicationsIntroduction:In various industrial sectors, the process of melting metals and other high-temperature applications plays a significant role. To ensure the success of these operations, the selection of high-quality equipment is essential. Graphite crucibles, popularly used for melting purposes, have gained immense popularity due to their exceptional properties and reliability. In this blog post, we will delve into the features, benefits, and applications of graphite crucibles for melting various materials in industrial settings.1. Understanding Graphite Crucibles:Graphite crucibles are specialized containers designed for holding and melting metals and other materials at extremely high temperatures. These crucibles are made from high-purity graphite, which exhibits remarkable thermal conductivity, corrosion resistance, and mechanical strength. The unique properties of graphite make it an ideal material for melting purposes.2. Key Features of Graphite Crucibles:2.1 High Thermal Conductivity:Graphite crucibles offer excellent heat transfer capabilities. Their high thermal conductivity ensures efficient and uniform melting of metals, eliminating the formation of hotspots, and providing consistent results.2.2 Corrosion Resistance:The chemical inertness of graphite makes crucibles highly resistant to corrosive agents. They can withstand aggressive molten materials, preventing contamination and maintaining the purity of the melted substance.2.3 Mechanical Strength:Graphite crucibles possess exceptional mechanical strength, allowing them to endure high temperatures and withstand thermal shock. This durability ensures longevity and enables multiple reuse cycles, making them a cost-effective choice.2.4 Excellent Insulation:Graphite crucibles exhibit excellent insulation properties, minimizing heat loss during melting operations. This feature increases energy efficiency and reduces operating costs.3. Benefits of Using Graphite Crucibles for Melting:3.1 Versatility:Graphite crucibles are compatible with a wide range of metals and materials. From precious metals like gold and silver to high-temperature alloys, graphite crucibles offer versatility for diverse melting requirements.3.2 Clean and Contamination-Free Melting:The non-reactive nature of graphite minimizes unwanted reactions, ensuring clean and pure melting processes. This aspect is crucial in industries like jewelry-making, where precise composition and flawless quality are imperative.3.3 Cost-Effective Solution:Graphite crucibles are highly durable and can withstand repeated use, making them a cost-effective solution in the long run. Additionally, their exceptional thermal conductivity reduces melting time and energy consumption, further contributing to cost savings.3.4 Easy Handling and Maintenance:Graphite crucibles are lightweight and easy to handle, simplifying the overall melting process and reducing the operational burden. Basic maintenance practices like periodic cleaning ensure the longevity of these crucibles.4. Applications of Graphite Crucibles:4.1 Metallurgy and Foundry:Graphite crucibles find extensive usage in the metallurgical and foundry industries for melting and casting various metals such as iron, steel, aluminum, and copper. Their thermal resistance and durability make them an ideal choice in these demanding operations.4.2 Jewelry-Making:The jewelry industry relies heavily on graphite crucibles for melting precious metals, enabling the creation of intricate and high-quality jewelry designs. The purity maintained during melting ensures flawless end products.4.3 Laboratory Applications:Graphite crucibles are widely employed in laboratory settings for experiments requiring high temperatures and controlled melting processes. Their reliability and consistency make them a trusted choice for scientific research and analysis.Conclusion:Graphite crucibles are a reliable and efficient solution for melting operations in diverse industries. Their exceptional properties, including high thermal conductivity, corrosion resistance, and mechanical strength, make them ideal for applications ranging from foundries to jewelry-making and laboratory experiments. With their cost-effectiveness and versatility, graphite crucibles continue to be the go-to choice for achieving efficient and contamination-free melting processes.