High-quality Extruded Graphite Block for Various Industrial Applications
By:Admin
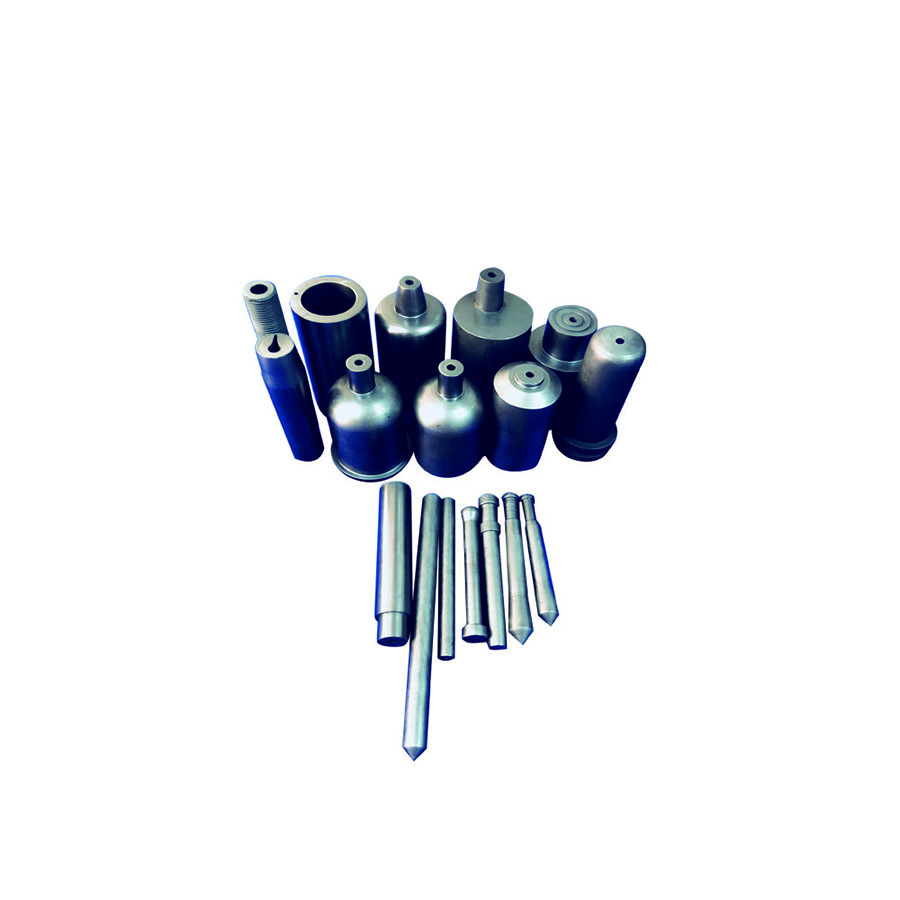
{City, Date} - {Company Name}, a leading manufacturer of advanced materials, has introduced a new extruded graphite block for industrial applications. This new product is expected to revolutionize the industry with its superior performance, durability, and versatility.
Extruded graphite blocks are widely used in various industries, including aerospace, automotive, electronics, and manufacturing. They are essential for applications such as heat exchangers, molds, crucibles, and various other thermal management processes. The high demand for extruded graphite blocks has driven {Company Name} to develop a product that meets the evolving needs of the industry.
The newly introduced extruded graphite block by {Company Name} is engineered to offer unparalleled thermal conductivity, high temperature resistance, and excellent machinability. These key features make it an ideal choice for critical applications where precision and reliability are essential.
{Company Name} has built a strong reputation for delivering innovative solutions to meet the specific requirements of its customers. With the introduction of this new extruded graphite block, the company is set to further strengthen its position in the market as a trusted partner for advanced materials.
The extruded graphite block is manufactured using state-of-the-art technology and high-quality raw materials to ensure consistent, reliable performance. Its unique composition allows for excellent thermal stability, making it suitable for extreme temperature environments. Additionally, the block is designed to withstand high mechanical loads, making it a durable and long-lasting solution for industrial applications.
In addition to its exceptional physical properties, the extruded graphite block from {Company Name} also offers excellent chemical resistance, making it compatible with a wide range of processing environments. This versatility makes it a valuable asset for industries where corrosion and chemical reactions are common challenges.
{Company Name} takes great pride in its commitment to environmental sustainability and responsible manufacturing practices. The new extruded graphite block is produced using eco-friendly processes, minimizing its environmental impact while maintaining the highest quality standards.
The company's dedication to customer satisfaction is reflected in its comprehensive technical support and services. {Company Name} offers customized solutions and expertise to help customers optimize the performance of the extruded graphite block in their specific applications. This personalized approach sets {Company Name} apart as a trusted partner for businesses seeking high-quality materials and technical support.
The introduction of the new extruded graphite block underscores {Company Name}'s relentless pursuit of excellence and innovation. The company continuously invests in research and development to push the boundaries of material science, enabling its customers to stay ahead in their respective industries.
As the global demand for advanced materials continues to grow, {Company Name} remains at the forefront of the industry, providing cutting-edge solutions that empower businesses to thrive in a competitive market. The new extruded graphite block is yet another testament to the company's commitment to driving progress and shaping the future of industrial applications.
In conclusion, {Company Name}'s new extruded graphite block represents a significant advancement in the field of advanced materials. With its superior performance, durability, and versatility, this product is poised to set new standards for industrial applications. As {Company Name} continues to innovate and expand its product offerings, it reaffirms its position as a leading provider of advanced materials that drive progress and empower businesses worldwide.
Company News & Blog
High-Quality Homemade Graphite Crucible for Various Applications
Homemade Graphite Crucible Revolutionizes the Foundry IndustryIn the world of metal casting, the crucible is an essential component that plays a critical role in the process of melting and pouring metals such as iron, steel, aluminum, and bronze. Traditionally, crucibles were manufactured using clay, silicon carbide, and other refractory materials, but recently, a new player has emerged in the foundry industry – a homemade graphite crucible that is revolutionizing the way metals are cast.The graphite crucible, created by a small, innovative company, has been making waves in the industry due to its unique properties and superior performance. Unlike traditional crucibles, which are often prone to cracking and have limited durability, the homemade graphite crucible offers exceptional thermal stability and resistance to thermal shock. This makes it an ideal choice for foundries looking to improve their casting processes and enhance the quality of their metal products.One of the key advantages of the homemade graphite crucible is its ability to withstand extreme temperatures, making it suitable for use with a wide range of metals and alloys. Its high thermal conductivity allows for rapid and uniform heating, ensuring efficient melting and pouring of metals. Additionally, the graphite material offers excellent chemical inertness, preventing the crucible from reacting with the molten metal and contaminating the final product.Furthermore, the homemade graphite crucible has proven to be highly durable and long-lasting, providing foundries with a cost-effective solution for their casting needs. Unlike traditional crucibles that require frequent replacement due to wear and tear, the graphite crucible can withstand prolonged use without compromising its performance. This not only reduces maintenance and replacement costs but also minimizes downtime, allowing foundries to maximize their productivity and output.In addition to its technical advantages, the homemade graphite crucible is also environmentally friendly. The production process of the crucible involves minimal waste and energy consumption, making it a sustainable option for foundries looking to reduce their environmental footprint. Furthermore, the crucible can be recycled after use, further minimizing its impact on the environment.The company behind the homemade graphite crucible takes pride in its commitment to innovation and quality. With a team of experienced engineers and metallurgists, the company has developed a range of graphite crucibles that are tailored to meet the specific needs of different foundries. Whether it's a small-scale operation or a large industrial foundry, the company offers custom solutions that are designed to maximize performance and efficiency.The success of the homemade graphite crucible has caught the attention of industry leaders and experts, who recognize its potential to transform the foundry industry. In a recent interview, the CEO of a leading foundry remarked, "The homemade graphite crucible has been a game-changer for our operation. It has significantly improved our casting processes, resulting in higher-quality products and increased efficiency."As the demand for high-quality metal products continues to grow, the homemade graphite crucible is poised to play a pivotal role in shaping the future of the foundry industry. Its unique combination of performance, durability, and sustainability has positioned it as a top choice for foundries seeking to stay ahead of the competition.In conclusion, the homemade graphite crucible has emerged as a disruptive force in the foundry industry, offering a new and improved alternative to traditional crucibles. With its superior performance, durability, and environmental benefits, the graphite crucible is set to revolutionize the way metals are cast, paving the way for a more efficient and sustainable future for foundries around the world.
Vacuum Metallizing Machine for Roll-to-Roll Production of Alloy Films on PET, BOPP, CPP, PVC, and Paper
Roll to Roll Alloy Film Vacuum Metallizing Machine for Pet BOPP CPP PVC Paper - Graphite Crucible for Vacuum Metallizing FilmVacuum metallizing is the process of depositing a thin film of metal onto a substrate, such as plastic, paper, or glass, in a vacuum environment. This process is widely used in various industries, including packaging, automotive, cosmetics, and electronics. In this blog post, we will discuss the Roll to Roll Alloy Film Vacuum Metallizing Machine for Pet BOPP CPP PVC Paper and the importance of using Graphite Crucibles in the vacuum metallizing process.Roll to Roll Alloy Film Vacuum Metallizing MachineThe Roll to Roll Alloy Film Vacuum Metallizing Machine for Pet BOPP CPP PVC Paper is a type of web vacuum coater designed to deposit a thin film of metal alloy onto a continuous roll of material such as plastic, paper, or fabric. This type of vacuum metallizing machine is widely used in the packaging industry for producing decorative and functional films for a range of packaging applications. The machine is equipped with a vacuum chamber, a metal alloy deposition system, and a roll-to-roll web transport system. The substrate material is fed from a roll into the vacuum chamber, where it is pre-treated and then coated with a thin layer of metal alloy. The metal alloy is vaporized and deposited onto the substrate in a thin, uniform layer. The Roll to Roll Alloy Film Vacuum Metallizing Machine for Pet BOPP CPP PVC Paper has several advantages over other deposition techniques. It can produce films with high uniformity and consistency, is cost-effective, and supports high-volume production. Graphite Crucibles for Vacuum Metallizing FilmGraphite Crucibles are an essential component of the vacuum metallizing process. They are used to hold the metal alloy and heat it until it vaporizes and is deposited onto the substrate. The graphite crucible serves as a container for the metal alloy, which is heated to a temperature at which it vaporizes. The vaporized metal alloy is then deposited onto the substrate in the vacuum chamber.Graphite Crucibles are ideal for vacuum metallizing because they can withstand high temperatures, are chemically inert, and have excellent thermal conductivity. The crucibles are designed to withstand the harsh conditions of the vacuum chamber and ensure that the metal alloy is heated and vaporized evenly.ConclusionThe Roll to Roll Alloy Film Vacuum Metallizing Machine for Pet BOPP CPP PVC Paper is a critical component of the packaging industry. It enables the production of high-quality, functional, and decorative films at scale. However, to achieve the desired effect, it is essential to use high-quality Graphite Crucibles. Graphite Crucibles are essential to the vacuum metallizing process as they help to ensure that the conditions in the vacuum chamber are optimal for the vaporization of the metal alloy and the deposition of the thin film. With high-quality Graphite Crucibles, manufacturers can produce high-quality, durable, and decorative films that meet the needs of their customers.
Exothermic Welding Moulds for Precise Welding - Graphite Material Available
Exothermic Welding Graphite Moulds: The Perfect Solution for WeldingExothermic welding, also known as exothermic bonding, thermit welding, or thermite welding, is a method of welding that uses heat generated by a chemical reaction to join two metals. This method of welding is widely used in various industries and applications, including construction and electrical work.One essential component of exothermic welding is the graphite mould used to contain and shape the weld. These moulds are essential to ensure a proper bond between the two metals and are available in different sizes and shapes to meet various welding needs.China is a leading manufacturer and supplier of exothermic welding graphite moulds. Chinese manufacturers offer high-quality moulds that meet international standards at affordable prices, making it an attractive option for businesses worldwide.CAD Exothermic Welding MouldsCAD exothermic welding moulds are a popular option among businesses looking for precise and efficient exothermic welding. These moulds are designed using computer-aided design (CAD) technology, enabling manufacturers to produce moulds with exact specifications.The use of CAD technology ensures that these moulds have a consistent and accurate shape, which results in a uniform weld. These moulds are also highly durable and can withstand high temperatures, ensuring they can be used repeatedly.Graphite Welding MouldsGraphite is a popular material used to manufacture exothermic welding moulds due to its ability to withstand high temperatures, which is essential in exothermic welding. Graphite moulds are also easy to handle, lightweight, and offer a high level of flexibility when it comes to shaping and designing them.Graphite welding moulds are highly durable, making them an excellent choice for businesses that rely on welding frequently. Graphite moulds are also easy to maintain, which makes them a cost-efficient option for businesses.Exothermic Weld MaterialThe exothermic weld material used in exothermic welding is a mixture of metal powder and a metal oxide, along with other compounds that help initiate the chemical reaction that creates the heat required for welding.The exothermic welding material is available in different sizes, depending on the size of the welding job, and can weld all types of conductors, including copper, brass, aluminum, steel, and others.ConclusionExothermic welding is an essential method of welding used in various industries worldwide. Graphite moulds and the exothermic weld material used in exothermic welding are two critical components that ensure the welding process works correctly.China is one of the leading manufacturers and suppliers of exothermic welding graphite moulds, which are known for their high quality, durability, and affordability. The use of CAD technology has made it possible for manufacturers to produce highly accurate and efficient moulds.Businesses that rely on exothermic welding should consider using China's graphite moulds and exothermic weld material to achieve the best welding results.
High-quality Graphite Crucible for Metallizing Film Production
Graphite Crucible for Metallizing Film: A Breakthrough in Metallizing TechnologyIn recent years, the demand for metallized films has been on the rise, driven by the growing need for high-performance packaging materials in various industries. Metallizing films are extensively used in applications such as food packaging, decorative materials, and electronic products. However, the manufacturing process of metallized films relies heavily on the use of graphite crucibles, which play a crucial role in the metallization process.One company that has been at the forefront of metallizing technology is a leading manufacturer and supplier of graphite crucibles. With a strong focus on innovation and quality, the company has developed a cutting-edge graphite crucible specifically designed for metallizing film applications. This breakthrough in metallizing technology is set to revolutionize the production of metallized films, offering enhanced performance and efficiency.The newly developed graphite crucible for metallizing film is engineered to meet the rigorous demands of the metallization process. It is manufactured using high-quality graphite material, ensuring excellent thermal conductivity, superior strength, and exceptional resistance to thermal shock. The crucible is designed to withstand the extreme temperatures and harsh operating conditions encountered during the metallization process, making it a reliable and durable solution for metallizing film manufacturers.In addition to its superior material properties, the graphite crucible is also optimized for efficient and uniform metallization. Its unique design features a smooth and homogeneous surface, which promotes even deposition of the metal coating onto the film substrate. This results in a high-quality metallized film with consistent thickness and excellent adhesion, meeting the stringent performance requirements of various end-use applications.Furthermore, the graphite crucible for metallizing film is available in a range of sizes and configurations to accommodate different production needs. Whether it is for small-scale lab testing or large-scale industrial production, the company offers a comprehensive selection of graphite crucibles to cater to diverse metallization requirements. Additionally, the company provides custom crucible design and manufacturing services, allowing tailored solutions to be developed based on specific customer needs and application demands.The development of the graphite crucible for metallizing film underscores the company's commitment to driving innovation in metallizing technology. By leveraging its expertise in graphite materials and process engineering, the company has successfully engineered a game-changing solution that promises to elevate the performance and efficiency of metallized film production. With a keen focus on quality and reliability, the company aims to empower metallizing film manufacturers with the tools they need to achieve superior results in their production processes.As a reputable and trusted supplier of graphite crucibles, the company has a proven track record of delivering high-performance solutions to the metallizing industry. Its extensive experience and technical capabilities enable the company to provide comprehensive support and expertise to customers, assisting them in optimizing their metallization processes and enhancing their product quality. The company's dedication to customer satisfaction and continuous improvement further solidifies its position as a leading provider of graphite crucibles for metallizing film applications.In conclusion, the introduction of the graphite crucible for metallizing film represents a significant advancement in metallizing technology. With its exceptional material properties, optimized design, and versatile offerings, the graphite crucible is poised to bring about a positive impact on the metallized film industry. As the company continues to drive innovation and excellence in metallizing technology, it is set to play a pivotal role in shaping the future of metallized film production, delivering value and performance to manufacturers and end-users alike.
Discover the Essential Functions and Applications of a Rotary Kiln
Title: Revolutionary Rotary Kiln Technology Poised to Transform the IndustryIntroduction:In a world constantly seeking more sustainable alternatives, the renowned engineering company {} is set to revolutionize the industry with their groundbreaking rotary kiln technology. Offering a comprehensive solution to address the challenges of traditional processes, their innovative rotary kiln design aims to significantly reduce carbon emissions, improve energy efficiency, and enhance the long-term sustainability of production across various sectors.Body:1. The Need for Innovations in Rotary Kiln Technology (150 words):The conventional rotary kiln has been widely used in industries like cement, minerals, and chemicals, among others, for decades. However, it inherently suffers from several shortcomings, including high energy consumption, significant greenhouse gas emissions, and limited operational flexibility. As the world increasingly prioritizes eco-friendliness and sustainability, there has been a growing demand for advanced technologies that can mitigate the environmental impact of manufacturing processes.2. Introducing the Revolutionary {} Rotary Kiln (150 words):{} has heeded this call for change by developing an exceptional rotary kiln technology that promises to reshape the industry. By incorporating cutting-edge engineering principles, this innovative design optimizes energy efficiency while drastically reducing carbon emissions. Transforming the conventional rotary kiln into an advanced and sustainable solution, the new design enables production plants to meet strict environmental regulations, achieve substantial cost savings, and enhance operational flexibility.3. Key Features and Benefits (200 words):The updated rotary kiln design integrates several game-changing features, elevating its performance and sustainability. A few significant highlights include:a. Enhanced Energy Efficiency: The {} rotary kiln utilizes advanced heat recovery systems and optimized insulation techniques, significantly improving thermal efficiency and reducing energy consumption. This leads to substantial cost savings and a more sustainable manufacturing process.b. Reduced Carbon Footprint: By effectively capturing and neutralizing harmful greenhouse gas emissions, the new rotary kiln technology helps industries make substantial progress towards achieving their carbon reduction goals. The design minimizes toxic pollutant discharge into the atmosphere, ensuring compliance with stringent environmental regulations.c. Operational Flexibility: {} rotary kiln technology offers remarkable flexibility, allowing for the processing of a wide range of materials, including cement, minerals, and even industrial waste. This versatility enables production plants to adapt quickly to changing market demands, minimizing downtime and maximizing operational efficiency.d. Enhanced Safety Features: The new rotary kiln design incorporates state-of-the-art safety measures, ensuring the well-being of workers while minimizing the risk of accidents or incidents during operation.4. Applications and Potential Impact (200 words):The profound impact of the revolutionary {} rotary kiln technology extends to a myriad of industries. Cement manufacturers can vastly reduce their carbon footprint and energy costs, while simultaneously increasing cement production capacity. Furthermore, the mineral processing industry can achieve greater efficiency and cost-effectiveness in extracting valuable minerals.Additionally, the steel industry can leverage this technology to improve energy efficiency and decrease carbon emissions in the production of iron ore pellets. Other potential applications include the treatment of hazardous waste and the production of alternative fuels from biomass and municipal solid waste, fostering a circular economy.5. Collaboration and Future Outlook (100 words):{} is actively seeking collaborative partnerships with industry leaders to further refine and implement their cutting-edge rotary kiln technology. By combining their technical expertise with the industry's demands, {} aims to continuously enhance their innovative solution and drive sustainability across various sectors globally.Conclusion:With the introduction of their revolutionary rotary kiln technology, {} has opened up a new era for the industry, providing a transformative approach to energy efficiency, reduced carbon emissions, and enhanced operational flexibility. As industries rapidly transition towards sustainability, this innovation stands poised to become the go-to solution, ensuring a greener and more efficient manufacturing landscape for generations to come.
Graphite Products Enhance Glass Fiber Strength and Durability
Title: Graphite Product Revolutionizes Glass Fiber Production ProcessIntroduction:In an era marked by rapid technological advancements, the materials used in manufacturing processes are continuously evolving. One remarkable innovation in the field of glass fiber production is the introduction of an exceptional graphite product. This groundbreaking development has been achieved through years of dedicated research and development by a leading company in the field. By leveraging the exceptional properties of this graphite product, they have successfully revolutionized the glass fiber production process, leading to enhanced efficiency, improved product quality, and cost-effectiveness.Company Introduction:Established in [year], [Company Name] has cemented its position as a pioneer in the manufacturing industry. With a focus on innovation and excellence, they have consistently pushed the boundaries of conventional practices. Their commitment to research and development has resulted in several groundbreaking products that have redefined industrial processes across multiple sectors. Leveraging a team of highly skilled professionals and state-of-the-art facilities, [Company Name] has consistently delivered solutions that address the evolving needs of global manufacturers.Graphite Product for Glass Fiber:[Company Name]'s newly developed graphite product for the glass fiber industry is a game-changer. This versatile material possesses exceptional properties that significantly augment the glass fiber production process. Its integration within this industry has the potential to transform the entire manufacturing landscape, boosting efficiency and ultimately driving growth.1. High Thermal Conductivity:The innovative graphite product demonstrates superior thermal conductivity, allowing for better control and management of the production process. By optimizing heat transfer at various stages, it ensures uniform heat distribution, reducing the risk of thermal inconsistencies and material defects. This breakthrough property of the graphite product leads to improved product quality and significantly minimizes manufacturing downtime.2. Enhanced Material Strength:Graphite's inherent strength and resistance to chemical corrosion enable it to withstand the demanding conditions encountered during the glass fiber production process. This reliability equates to longer product life, resulting in reduced downtime due to maintenance and repairs. Additionally, the longevity of the product translates into cost savings for manufacturers in the long run.3. Increased Productivity:By incorporating the graphite product into their production lines, glass fiber manufacturers have reported significant improvements in overall productivity. The material's exceptional lubricity ensures smooth and continuous operations, reducing the risk of equipment breakdown and hindrances. The reduced downtime and enhanced efficiency allow manufacturers to optimize their output, meet increasing market demands, and maintain a competitive edge.4. Environmentally Friendly:[Company Name]'s graphite product is also eco-friendly, aligning with the global trend towards sustainability. Its composition is free from harmful substances, diminishing the industry's environmental footprint. By adopting this innovative product, glass fiber manufacturers underscore their commitment to responsible production and sustainable practices.Conclusion:The integration of [Company Name]'s graphite product into the glass fiber production process represents a monumental advancement within the industry. With its exceptional thermal conductivity, enhanced material strength, increased productivity, and environmentally friendly properties, this revolutionary material offers unparalleled benefits to manufacturers. By reducing manufacturing downtime, improving product quality, and promoting sustainability, [Company Name]'s graphite product paves the way for a more efficient and sustainable glass fiber industry. The collaboration between [Company Name] and glass fiber manufacturers facilitates the realization of untapped potentials, ensuring an exciting and prosperous future for this sector.
High-quality Graphite Crucibles Ideal for Melting Tin
Title: Graphite Crucible for Melting: A Reliable Choice for Industrial ApplicationsIntroduction:In various industrial sectors, the process of melting metals and other high-temperature applications plays a significant role. To ensure the success of these operations, the selection of high-quality equipment is essential. Graphite crucibles, popularly used for melting purposes, have gained immense popularity due to their exceptional properties and reliability. In this blog post, we will delve into the features, benefits, and applications of graphite crucibles for melting various materials in industrial settings.1. Understanding Graphite Crucibles:Graphite crucibles are specialized containers designed for holding and melting metals and other materials at extremely high temperatures. These crucibles are made from high-purity graphite, which exhibits remarkable thermal conductivity, corrosion resistance, and mechanical strength. The unique properties of graphite make it an ideal material for melting purposes.2. Key Features of Graphite Crucibles:2.1 High Thermal Conductivity:Graphite crucibles offer excellent heat transfer capabilities. Their high thermal conductivity ensures efficient and uniform melting of metals, eliminating the formation of hotspots, and providing consistent results.2.2 Corrosion Resistance:The chemical inertness of graphite makes crucibles highly resistant to corrosive agents. They can withstand aggressive molten materials, preventing contamination and maintaining the purity of the melted substance.2.3 Mechanical Strength:Graphite crucibles possess exceptional mechanical strength, allowing them to endure high temperatures and withstand thermal shock. This durability ensures longevity and enables multiple reuse cycles, making them a cost-effective choice.2.4 Excellent Insulation:Graphite crucibles exhibit excellent insulation properties, minimizing heat loss during melting operations. This feature increases energy efficiency and reduces operating costs.3. Benefits of Using Graphite Crucibles for Melting:3.1 Versatility:Graphite crucibles are compatible with a wide range of metals and materials. From precious metals like gold and silver to high-temperature alloys, graphite crucibles offer versatility for diverse melting requirements.3.2 Clean and Contamination-Free Melting:The non-reactive nature of graphite minimizes unwanted reactions, ensuring clean and pure melting processes. This aspect is crucial in industries like jewelry-making, where precise composition and flawless quality are imperative.3.3 Cost-Effective Solution:Graphite crucibles are highly durable and can withstand repeated use, making them a cost-effective solution in the long run. Additionally, their exceptional thermal conductivity reduces melting time and energy consumption, further contributing to cost savings.3.4 Easy Handling and Maintenance:Graphite crucibles are lightweight and easy to handle, simplifying the overall melting process and reducing the operational burden. Basic maintenance practices like periodic cleaning ensure the longevity of these crucibles.4. Applications of Graphite Crucibles:4.1 Metallurgy and Foundry:Graphite crucibles find extensive usage in the metallurgical and foundry industries for melting and casting various metals such as iron, steel, aluminum, and copper. Their thermal resistance and durability make them an ideal choice in these demanding operations.4.2 Jewelry-Making:The jewelry industry relies heavily on graphite crucibles for melting precious metals, enabling the creation of intricate and high-quality jewelry designs. The purity maintained during melting ensures flawless end products.4.3 Laboratory Applications:Graphite crucibles are widely employed in laboratory settings for experiments requiring high temperatures and controlled melting processes. Their reliability and consistency make them a trusted choice for scientific research and analysis.Conclusion:Graphite crucibles are a reliable and efficient solution for melting operations in diverse industries. Their exceptional properties, including high thermal conductivity, corrosion resistance, and mechanical strength, make them ideal for applications ranging from foundries to jewelry-making and laboratory experiments. With their cost-effectiveness and versatility, graphite crucibles continue to be the go-to choice for achieving efficient and contamination-free melting processes.
Innovative Graphite Technology Revolutionizes Sintering Mould for Industry Applications
Graphite Sintering Moulds Revolutionize Manufacturing Processes(Graphite Company Name), a leading innovator in the field of advanced materials and manufacturer of cutting-edge graphite products, has recently introduced a groundbreaking new product - Graphite Sintering Moulds. These molds are set to revolutionize manufacturing processes across various industries, providing enhanced durability, heat resistance, and improved production efficiency.(Graphite Company Name) has been at the forefront of graphite-based innovations for over a decade, catering to the needs of industries such as automotive, aerospace, electronics, and more. With a dedicated research and development team, their focus has always been on developing advanced materials that push the boundaries of what is possible.The recently launched Graphite Sintering Moulds are the latest addition to (Graphite Company Name)'s extensive product portfolio. Traditionally, manufacturing processes involving high temperatures and pressure require molds that can withstand these extreme conditions. This is where Graphite Sintering Moulds come into play.One of the key advantages of these molds is their exceptional durability. Graphite, already known for its strength and resilience, has been further optimized in the development of these molds to withstand extreme heat conditions. This means that manufacturers can now produce high-quality, complex components without having to constantly worry about mold degradation due to high temperatures.Furthermore, the heat resistance of Graphite Sintering Moulds significantly reduces the cooling time required during the manufacturing process. The molds dissipate heat quickly and evenly, allowing for a rapid cooling process. This translates into increased production efficiency as manufacturers can achieve shorter cycle times, ultimately leading to higher productivity and reduced costs.In addition to their durability and heat resistance, these molds also offer excellent thermal conductivity. This unique property allows for more uniform heat distribution, resulting in consistent product quality and minimal defects. Manufacturers can rely on Graphite Sintering Moulds to deliver precise and reliable results, meeting the stringent requirements of various industries.Another notable advantage of Graphite Sintering Moulds is their versatility. These molds can be used in a wide range of manufacturing processes, including powder metallurgy, metal injection molding, and ceramic sintering. They have proven to be particularly effective in industries where the production of intricate and delicate components is required. The use of these molds enables precise replication of complex designs, ensuring consistent quality across batches.(Graphite Company Name)'s commitment to sustainability is also reflected in the development of these molds. Graphite is a naturally occurring mineral, and by utilizing it in manufacturing processes, the company minimizes the environmental impact associated with conventional mold materials. Additionally, the long lifespan of Graphite Sintering Moulds reduces the need for frequent replacements, further reducing waste generation.To cater to the diverse needs of their clients, (Graphite Company Name) offers customization options for their Graphite Sintering Moulds. The molds can be tailored to specific requirements, including sizes, shapes, and surface finishes. This flexibility allows manufacturers to optimize their production processes and achieve superior end-products.Overall, the introduction of Graphite Sintering Moulds represents a significant advancement in manufacturing technology. By providing exceptional durability, heat resistance, and thermal conductivity, these molds empower manufacturers to improve production efficiency and achieve consistent product quality. With their commitment to innovation and sustainability, (Graphite Company Name) continues to set new industry standards, driving progress and revolutionizing manufacturing processes across various sectors.
High-Quality Carbon Graphite Casting Moulds for Effective Casting Operations
Carbon Graphite Casting Mould - A Breakthrough in Manufacturing TechnologyInnovations in manufacturing technology have always been a driving force behind the advancement of various industries. One such innovative product that has recently gained attention is the Carbon Graphite Casting Mould, which is revolutionizing the way in which complex parts and components are produced.The Carbon Graphite Casting Mould, developed by a leading company in the manufacturing industry, is designed to address the challenges of producing high-quality, intricate components for a wide range of applications. The mould is made from high-quality carbon graphite material, which is known for its exceptional strength, durability, and thermal resistance. This makes it an ideal choice for casting moulds, as it can withstand the extreme temperatures and pressures involved in the casting process.The use of carbon graphite in the manufacturing of casting moulds offers a number of advantages over traditional materials such as steel and aluminum. Carbon graphite is significantly lighter than steel, which makes it easier to handle and transport. Additionally, it has a low coefficient of thermal expansion, which means that it remains dimensionally stable at high temperatures, resulting in minimal distortion or warping during the casting process.Furthermore, the exceptional thermal conductivity of carbon graphite allows for faster and more uniform heat distribution, leading to better casting results and reduced cycle times. This ultimately translates to improved productivity and cost savings for manufacturers.The Carbon Graphite Casting Mould is also well-suited for producing complex and intricate parts with fine details and intricate geometries. Its ability to withstand high temperatures and pressures allows for the precise replication of intricate features, leading to superior casting quality and dimensional accuracy.In addition to its exceptional material properties, the company behind the Carbon Graphite Casting Mould also offers a range of customization options to meet the specific needs of different applications. This includes the ability to tailor the mould's design, dimensions, and surface finishes to achieve optimal casting results for a variety of components.The use of Carbon Graphite Casting Mould is already making an impact across various industries, including automotive, aerospace, and industrial manufacturing. The mould has been successfully employed in the production of critical components such as engine parts, turbine blades, and intricate metallic structures, where the demand for high-performance and complex geometries is paramount.The adoption of Carbon Graphite Casting Mould has also been lauded for its positive environmental impact. The lightweight and durable nature of carbon graphite reduces the overall material usage and energy consumption in the manufacturing process, contributing to a greener and more sustainable production practice.As the manufacturing industry continues to evolve, innovative solutions such as the Carbon Graphite Casting Mould will play a crucial role in meeting the growing demand for high-performance and complex components. With its exceptional material properties, customization options, and environmental benefits, the mould is set to become an indispensable tool for manufacturers seeking to push the boundaries of what is possible in the realm of casting technology.In conclusion, the Carbon Graphite Casting Mould represents a significant advancement in manufacturing technology, offering a range of benefits including improved casting quality, enhanced productivity, and environmental sustainability. With its widespread applicability across different industries, it is poised to redefine the way complex components are produced, setting new standards for quality and efficiency in the manufacturing sector.
Small Electric Foundry for Bronze Casting: Tips and Techniques for Successful Results
Electric Foundry for Small Bronze Casting – Crucible for Melting BronzeBronze casting has been around for thousands of years. It is an ancient method of creating beautiful objects of art. Today, modern technology has made it easier for people to attempt bronze casting on their own. This is where a small electric foundry comes in handy. In this article, we will discuss how to make a small foundry for melting tin bronze.First, let's talk about the materials we will need. The following items are essential for building a small foundry:1. Soft fire bricks – These bricks are used to build the walls of the foundry. They are designed to withstand high temperatures.2. Insulator – This is a high-temperature insulation material that is used to line the inside of the foundry. It keeps the heat inside the foundry and prevents it from escaping.3. Nichrome coil – This is a heating element that is used to provide the heat needed to melt the tin bronze.4. Crucible – This is a container used to melt the bronze. It must be made of a material that can withstand high temperatures and is resistant to corrosion.Now that we have the materials, let's get started on building the foundry. The first step is to build a frame with the soft fire bricks. The size of the frame will depend on the size of the crucible. The frame should be built to support the crucible and the insulator.Next, place the insulator inside the frame. The insulator should be cut to size and placed inside the frame. It should be wrapped around the sides and the bottom of the frame. The insulator is what will keep the heat inside the foundry.After the insulator is in place, wrap the nichrome coil around the outside of the insulator. The coil should be wrapped tightly and evenly around the entire foundry. It should be wired to a 240V 10amp socket. The coil is what will provide the heat necessary to melt the tin bronze.Once the coil is in place, it's time to add the crucible. The crucible should be placed inside the foundry and centered on the coil. It should be large enough to hold the amount of bronze you plan to melt. The crucible should be made of a material that can withstand high temperatures, such as graphite or ceramic.Finally, turn on the power to the coil. The heat should be gradually increased until the bronze is fully melted. Once the bronze is melted, it's ready for casting.ConclusionBuilding a small foundry for melting tin bronze is not a difficult task. With the right materials, it can be done easily at home. By using a soft fire brick frame, high-temperature insulation, a nichrome coil, and a crucible, you can create your own electric foundry. This will allow you to create beautiful bronze objects of art in the comfort of your own home. So, get started today and let your creativity flow!