Geological Drilling Graphite Mould: The Ultimate Guide
By:Admin
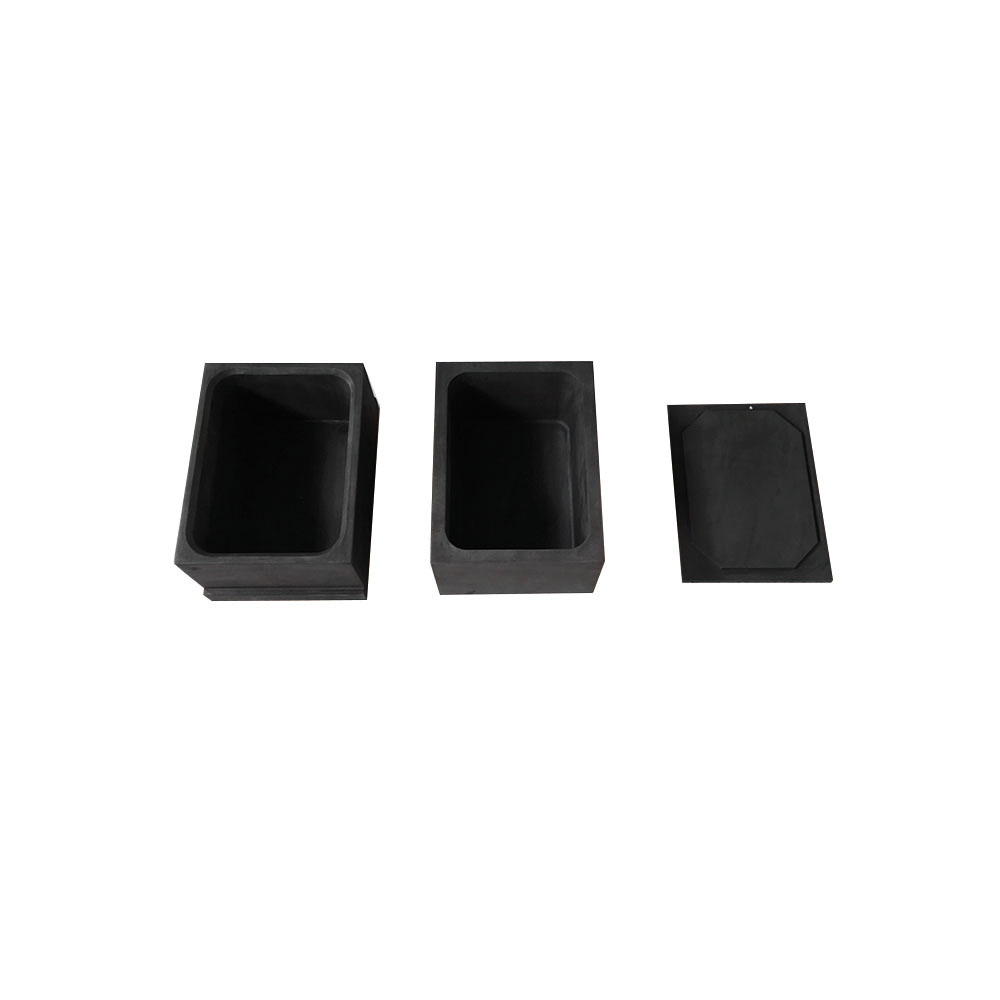
Geological drilling is a crucial part of the exploration and extraction process in the mining industry. The success of these drilling operations often relies on the quality of the equipment and tools used. One company at the forefront of the industry, [Company Name], has recently implemented a new graphite mould technology to enhance the performance and efficiency of its geological drilling operations.
[Company Name] is a leading provider of geological drilling services, specializing in mineral exploration, geotechnical drilling, and environmental investigations. With a strong focus on innovation and continuous improvement, the company is always on the lookout for new technologies and tools that can improve its operations.
The company recently identified the potential of graphite moulds in enhancing the performance of its drilling equipment. Graphite is known for its high thermal stability, low friction, and excellent machinability, making it an ideal material for creating precision components for drilling tools.
After extensive research and testing, [Company Name] successfully integrated graphite moulds into its drilling equipment, and the results have been impressive. The new graphite moulds have significantly improved the performance and durability of the drilling tools, leading to increased efficiency and productivity in the field.
The use of graphite moulds has allowed [Company Name] to achieve higher drilling speeds, reduce tool wear and tear, and improve overall drilling accuracy. These benefits have not gone unnoticed by the company's clients, who have praised the improved quality of the drilling operations.
In addition to the operational benefits, the use of graphite moulds has also had a positive environmental impact. The reduction in tool wear has led to less frequent replacements and a decrease in the amount of waste generated from old drilling equipment.
Furthermore, the use of graphite moulds has helped [Company Name] reduce its overall maintenance costs, as the durability of the tools has significantly increased. This has translated into cost savings for the company and its clients, making the drilling operations more cost-effective in the long run.
The success of the graphite mould implementation has solidified [Company Name]'s position as an industry leader in technological innovation. By continuously seeking out and adopting new technologies, the company has demonstrated its commitment to providing the highest quality services to its clients.
Looking ahead, [Company Name] is exploring additional applications for graphite moulds in its other drilling operations. The company is also open to collaborating with graphite mould manufacturers to further optimize the use of this technology and unlock its full potential in the field of geological drilling.
Overall, the integration of graphite moulds into [Company Name]'s drilling equipment has been a game-changer for the company and the industry as a whole. The technology has not only improved the performance and efficiency of the drilling operations but has also demonstrated the company's dedication to staying at the forefront of technological advancements in the field.
Company News & Blog
Discover the Essential Functions and Applications of a Rotary Kiln
Title: Revolutionary Rotary Kiln Technology Poised to Transform the IndustryIntroduction:In a world constantly seeking more sustainable alternatives, the renowned engineering company {} is set to revolutionize the industry with their groundbreaking rotary kiln technology. Offering a comprehensive solution to address the challenges of traditional processes, their innovative rotary kiln design aims to significantly reduce carbon emissions, improve energy efficiency, and enhance the long-term sustainability of production across various sectors.Body:1. The Need for Innovations in Rotary Kiln Technology (150 words):The conventional rotary kiln has been widely used in industries like cement, minerals, and chemicals, among others, for decades. However, it inherently suffers from several shortcomings, including high energy consumption, significant greenhouse gas emissions, and limited operational flexibility. As the world increasingly prioritizes eco-friendliness and sustainability, there has been a growing demand for advanced technologies that can mitigate the environmental impact of manufacturing processes.2. Introducing the Revolutionary {} Rotary Kiln (150 words):{} has heeded this call for change by developing an exceptional rotary kiln technology that promises to reshape the industry. By incorporating cutting-edge engineering principles, this innovative design optimizes energy efficiency while drastically reducing carbon emissions. Transforming the conventional rotary kiln into an advanced and sustainable solution, the new design enables production plants to meet strict environmental regulations, achieve substantial cost savings, and enhance operational flexibility.3. Key Features and Benefits (200 words):The updated rotary kiln design integrates several game-changing features, elevating its performance and sustainability. A few significant highlights include:a. Enhanced Energy Efficiency: The {} rotary kiln utilizes advanced heat recovery systems and optimized insulation techniques, significantly improving thermal efficiency and reducing energy consumption. This leads to substantial cost savings and a more sustainable manufacturing process.b. Reduced Carbon Footprint: By effectively capturing and neutralizing harmful greenhouse gas emissions, the new rotary kiln technology helps industries make substantial progress towards achieving their carbon reduction goals. The design minimizes toxic pollutant discharge into the atmosphere, ensuring compliance with stringent environmental regulations.c. Operational Flexibility: {} rotary kiln technology offers remarkable flexibility, allowing for the processing of a wide range of materials, including cement, minerals, and even industrial waste. This versatility enables production plants to adapt quickly to changing market demands, minimizing downtime and maximizing operational efficiency.d. Enhanced Safety Features: The new rotary kiln design incorporates state-of-the-art safety measures, ensuring the well-being of workers while minimizing the risk of accidents or incidents during operation.4. Applications and Potential Impact (200 words):The profound impact of the revolutionary {} rotary kiln technology extends to a myriad of industries. Cement manufacturers can vastly reduce their carbon footprint and energy costs, while simultaneously increasing cement production capacity. Furthermore, the mineral processing industry can achieve greater efficiency and cost-effectiveness in extracting valuable minerals.Additionally, the steel industry can leverage this technology to improve energy efficiency and decrease carbon emissions in the production of iron ore pellets. Other potential applications include the treatment of hazardous waste and the production of alternative fuels from biomass and municipal solid waste, fostering a circular economy.5. Collaboration and Future Outlook (100 words):{} is actively seeking collaborative partnerships with industry leaders to further refine and implement their cutting-edge rotary kiln technology. By combining their technical expertise with the industry's demands, {} aims to continuously enhance their innovative solution and drive sustainability across various sectors globally.Conclusion:With the introduction of their revolutionary rotary kiln technology, {} has opened up a new era for the industry, providing a transformative approach to energy efficiency, reduced carbon emissions, and enhanced operational flexibility. As industries rapidly transition towards sustainability, this innovation stands poised to become the go-to solution, ensuring a greener and more efficient manufacturing landscape for generations to come.
High-Quality Edm Mold for Graphite: What You Need to Know
Graphite EDM Mold: A Cutting-Edge Solution for Precision ManufacturingIn today’s fast-paced manufacturing industry, precision and efficiency are paramount. Companies are constantly seeking innovative solutions to stay ahead of the competition, and one such solution that has been garnering attention is the Graphite EDM Mold. This cutting-edge technology is revolutionizing the way manufacturers produce intricate and complex parts, and it is quickly becoming a staple in the arsenal of high-tech manufacturing companies.The Graphite EDM Mold is a precision tool used in electrical discharge machining (EDM) processes, which involves using electrical discharges to shape and produce intricate parts from hard metals and materials. The mold is made from high-quality graphite, which is an ideal material for EDM applications due to its high thermal conductivity and ability to withstand high temperatures.One company that has been at the forefront of developing and producing Graphite EDM Mold is {Company Name}. With over 20 years of experience in the manufacturing industry, {Company Name} has established itself as a leading provider of advanced tooling solutions for a wide range of industries, including aerospace, automotive, medical, and more. Their commitment to innovation and quality has led to the development of the Graphite EDM Mold, which has become a game-changer for manufacturers looking to produce intricate and high-precision parts.The Graphite EDM Mold offers several key advantages over traditional tooling solutions. Its high thermal conductivity allows for efficient heat dissipation during the EDM process, which results in improved surface finish and dimensional accuracy of the machined parts. Additionally, the inherent strength and stability of graphite make the mold highly durable and resistant to wear, resulting in longer tool life and reduced production downtime for tool changes.Furthermore, the Graphite EDM Mold is highly customizable and can be tailored to meet the specific needs of different applications and industries. {Company Name} offers a range of customization options, including varying graphite grades, electrode geometries, and surface finishes, to ensure that their customers can achieve the desired machining results for their unique parts.The use of Graphite EDM Mold has brought about a paradigm shift in the way manufacturers approach the production of complex and precision parts. With its ability to achieve tight tolerances and intricate geometries, the mold has opened up new possibilities for designing and manufacturing parts that were previously deemed too challenging or costly to produce.The aerospace industry, in particular, has embraced the Graphite EDM Mold as a critical tool for producing components with stringent tolerances and complex geometries. From turbine blades to fuel nozzles, manufacturers in the aerospace sector have turned to this advanced tooling solution to achieve the level of precision and quality required for their critical components.In the medical industry, the Graphite EDM Mold has also become instrumental in the production of intricate surgical instruments and implants. The mold’s ability to produce intricate and complex shapes with high precision has enabled manufacturers to push the boundaries of what is possible in terms of design and functionality for medical devices.Looking ahead, the future of Graphite EDM Mold looks promising, with continued advancements in materials and manufacturing techniques. As the demand for high-precision components continues to grow across various industries, the role of the Graphite EDM Mold is expected to expand even further, driving innovation and pushing the boundaries of what can be achieved in precision manufacturing.In conclusion, the Graphite EDM Mold has emerged as a cutting-edge solution for precision manufacturing, offering unparalleled capabilities to produce intricate and complex parts with high precision and efficiency. With {Company Name} at the helm of its development and production, the mold is poised to revolutionize the manufacturing industry and pave the way for new possibilities in design and production. As the demand for high-precision components continues to grow, the Graphite EDM Mold is set to play an increasingly pivotal role in shaping the future of manufacturing.
Exploring the Applications and Advantages of Graphite Stirring Rods
Graphite Stirring Rod: Advancing Industrial Processes with Superior PerformanceInnovative materials and tools are the backbone of technological advancements in various industries. One such breakthrough in the world of manufacturing and chemical processes is the Graphite Stirring Rod, a remarkable tool known for its superior performance. Deployed in diverse sectors, this tool is revolutionizing industrial processes, enabling companies to achieve higher efficiency, cost-effectiveness, and improved product quality. This article explores the limitless possibilities of this groundbreaking tool and the company behind its exceptional design and manufacturing.Graphite, a form of carbon, possesses exceptional properties that make it an ideal material for a wide range of applications. Its high melting point, superior thermal and electrical conductivity, and excellent chemical resistance make it an invaluable resource for various industrial processes. The Graphite Stirring Rod harnesses these properties to overcome traditional limitations and provide unparalleled performance in mixing, blending, and stirring applications.At the forefront of producing high-quality graphite stirring rods is a leading company that has pioneered the manufacture and development of advanced carbon-based products. With a legacy of excellence spanning several decades, their relentless pursuit of perfection and commitment to technological innovation have propelled them to the forefront of the industry.The company's state-of-the-art manufacturing facilities are equipped with cutting-edge technologies, enabling the production of graphite stirring rods with unmatched precision, consistency, and reliability. Their team of experts, comprising engineers and materials scientists, continually work towards refining their manufacturing processes and leveraging the latest advancements in material science. This dedication to staying ahead of the technological curve ensures the delivery of top-of-the-line products that cater to the evolving needs of diverse industries.The Graphite Stirring Rod, produced by this company, stands out due to its exceptional design and performance-enhancing features. Its unique composition and surface properties allow for efficient mixing and stirring of various substances, including liquids, powders, and viscoelastic materials. With its exceptional heat resistance and minimal reaction tendencies, the rod ensures the complete eradication of impurities while preventing product contamination, making it an indispensable tool in critical industries such as pharmaceuticals and food processing.The versatility of the Graphite Stirring Rod extends beyond its unrivaled performance in mixing and stirring applications. Its robustness and durability enable its usage in extreme environments and aggressive chemical processes. The rod's high thermal conductivity ensures efficient heat transfer, facilitating temperature control during reactions. Additionally, its electrical conductivity makes it suitable for applications requiring grounding or electrochemical reactions, thus amplifying its range of applications across various industries.In an era driven by sustainability and energy efficiency, the Graphite Stirring Rod possesses several environmentally-friendly attributes. The rod's long lifespan and resistance to corrosion and degradation significantly reduce waste generation and maintenance costs. Furthermore, the manufacturing process prioritizes eco-friendly practices, minimizing carbon footprint and promoting responsible consumption.The applications of the Graphite Stirring Rod span across multiple industries, including pharmaceuticals, chemicals, food processing, research laboratories, and energy production. In the pharmaceutical sector, this tool ensures the homogeneity of drug formulations, leading to increased efficacy and patient safety. In chemical processes, it aids in achieving uniformity and facilitating reactions, resulting in improved product quality and reduced waste. The food processing industry benefits from this tool's hygienic properties, assuring contamination-free production processes.In conclusion, the revolutionary Graphite Stirring Rod, manufactured by the leading carbon-based products company, has transformed industrial processes across various sectors. With its unparalleled performance, durability, and environmentally-friendly attributes, this exceptional tool exemplifies the potential of innovative materials in advancing technological capabilities. As this tool continues to redefine industry standards, companies across the globe are poised to benefit from its exceptional performance and optimized processes.
Innovative Porous Coating Graphite Mould: A New Advancement in Mould Technology
Porous Coating Graphite Mould has become an essential tool in the manufacturing industry, revolutionizing the way manufacturers create complex and intricate metal parts. The innovative technology behind Porous Coating Graphite Mould is making waves in the industry, providing manufacturers with a cost-effective and efficient solution for producing high-quality metal parts.With a history of over 20 years in the industry, {Company Name} has established itself as a leader in the production and distribution of Porous Coating Graphite Mould. The company has a strong focus on research and development, constantly striving to improve its products and stay ahead of the curve in terms of technological advancements. This commitment to innovation has allowed {Company Name} to become a trusted partner for manufacturers looking to improve their production processes.Porous Coating Graphite Mould is a versatile tool that can be used in a wide range of manufacturing applications. Whether it's producing automotive parts, aerospace components, or medical devices, Porous Coating Graphite Mould offers manufacturers the flexibility and precision they need to meet their production demands. The technology works by allowing gas to pass through the mould, which results in a uniform and consistent coating on the metal part being produced. This ensures that the final product has a smooth and flawless surface finish, free from imperfections or defects.One of the key advantages of using Porous Coating Graphite Mould is its ability to produce complex and intricate metal parts with high precision. This is particularly important in industries such as aerospace and medical manufacturing, where the smallest flaw in a part can have serious consequences. By using Porous Coating Graphite Mould, manufacturers can ensure that their parts meet the highest quality standards, while also reducing production time and costs.In addition to its precision and versatility, Porous Coating Graphite Mould also offers cost savings for manufacturers. The technology allows for a more efficient use of materials, reducing waste and minimizing the need for additional finishing processes. This results in lower production costs and a more sustainable manufacturing process overall.{Company Name} is committed to providing its customers with the highest quality Porous Coating Graphite Mould, backed by exceptional customer service and support. The company works closely with its clients to understand their specific production needs and develop customized solutions to meet those requirements. With a team of experienced engineers and technical experts, {Company Name} is able to provide comprehensive support to its customers, from initial consultation to ongoing maintenance and support.As the manufacturing industry continues to evolve and demand for high-quality metal parts grows, Porous Coating Graphite Mould is set to play a crucial role in shaping the future of manufacturing. With its precision, versatility, and cost-saving benefits, this innovative technology is helping manufacturers stay ahead of the curve and meet the ever-increasing demands of their customers. And with {Company Name} at the forefront of this technological revolution, manufacturers can trust that they have a reliable partner to support their production needs.
Geological Drilling Graphite Mould: The Ultimate Guide
Geological Drilling Company Utilizes Graphite Mould for Enhanced PerformanceGeological drilling is a crucial part of the exploration and extraction process in the mining industry. The success of these drilling operations often relies on the quality of the equipment and tools used. One company at the forefront of the industry, [Company Name], has recently implemented a new graphite mould technology to enhance the performance and efficiency of its geological drilling operations.[Company Name] is a leading provider of geological drilling services, specializing in mineral exploration, geotechnical drilling, and environmental investigations. With a strong focus on innovation and continuous improvement, the company is always on the lookout for new technologies and tools that can improve its operations.The company recently identified the potential of graphite moulds in enhancing the performance of its drilling equipment. Graphite is known for its high thermal stability, low friction, and excellent machinability, making it an ideal material for creating precision components for drilling tools.After extensive research and testing, [Company Name] successfully integrated graphite moulds into its drilling equipment, and the results have been impressive. The new graphite moulds have significantly improved the performance and durability of the drilling tools, leading to increased efficiency and productivity in the field.The use of graphite moulds has allowed [Company Name] to achieve higher drilling speeds, reduce tool wear and tear, and improve overall drilling accuracy. These benefits have not gone unnoticed by the company's clients, who have praised the improved quality of the drilling operations.In addition to the operational benefits, the use of graphite moulds has also had a positive environmental impact. The reduction in tool wear has led to less frequent replacements and a decrease in the amount of waste generated from old drilling equipment.Furthermore, the use of graphite moulds has helped [Company Name] reduce its overall maintenance costs, as the durability of the tools has significantly increased. This has translated into cost savings for the company and its clients, making the drilling operations more cost-effective in the long run.The success of the graphite mould implementation has solidified [Company Name]'s position as an industry leader in technological innovation. By continuously seeking out and adopting new technologies, the company has demonstrated its commitment to providing the highest quality services to its clients.Looking ahead, [Company Name] is exploring additional applications for graphite moulds in its other drilling operations. The company is also open to collaborating with graphite mould manufacturers to further optimize the use of this technology and unlock its full potential in the field of geological drilling.Overall, the integration of graphite moulds into [Company Name]'s drilling equipment has been a game-changer for the company and the industry as a whole. The technology has not only improved the performance and efficiency of the drilling operations but has also demonstrated the company's dedication to staying at the forefront of technological advancements in the field.
High-quality Graphite Box for Anode Powder: A Complete Guide
Graphite Box For Anode Powder - A Step Towards Sustainable Battery ProductionThe demand for lithium-ion batteries is rapidly increasing with the growing popularity of electric vehicles, portable electronic devices, and energy storage systems. To meet this demand, the production of anode powder, a key component of lithium-ion batteries, is also rising. However, the traditional methods of producing anode powder are often associated with high energy consumption and environmental impact. In response to this challenge, {company name} has developed a sustainable solution - the Graphite Box for Anode Powder - that aims to revolutionize the battery production industry.{company name} is a leading manufacturer of advanced materials for various industries, including energy storage, electronics, and aerospace. The company has a strong focus on research and development, aiming to create innovative solutions that address the environmental and sustainability challenges of modern industries. The Graphite Box for Anode Powder is one such innovation that showcases {company name}'s commitment to sustainable manufacturing practices.The Graphite Box for Anode Powder is designed to improve the production process of anode powder by utilizing graphite as a crucial component. Graphite is known for its exceptional thermal and electrical conductivity, making it an ideal material for high-temperature applications such as the production of anode powder. The box is specifically engineered to provide a controlled environment for the synthesis of anode powder, ensuring high quality and consistency in the final product.One of the key advantages of the Graphite Box for Anode Powder is its energy efficiency. Traditional methods of anode powder production often involve high-temperature processes that consume a significant amount of energy. In contrast, {company name}'s innovative solution minimizes energy consumption by utilizing the thermal conductivity of graphite to maintain the required temperature within the production environment. This not only reduces the operational costs for manufacturers but also contributes to a more sustainable and eco-friendly production process.Furthermore, the use of the Graphite Box for Anode Powder contributes to the reduction of greenhouse gas emissions in the production of lithium-ion batteries. As the global focus on sustainability and environmental impact intensifies, manufacturers are increasingly seeking innovative solutions to minimize their carbon footprint. The implementation of the Graphite Box for Anode Powder aligns with this trend, offering a more sustainable approach to battery production that supports the broader goal of mitigating climate change.In addition to its environmental benefits, the Graphite Box for Anode Powder also enhances the performance and reliability of lithium-ion batteries. The controlled production environment ensures the uniformity and purity of the anode powder, ultimately leading to improved battery performance and longevity. This is particularly significant in the context of electric vehicles and energy storage systems, where the reliability and efficiency of lithium-ion batteries are critical for the overall performance of the applications.{company name} aims to collaborate with battery manufacturers and research institutions to further optimize the Graphite Box for Anode Powder and promote its widespread adoption across the industry. By partnering with key stakeholders, {company name} seeks to drive innovation in battery production and contribute to the advancement of sustainable energy technologies.In conclusion, the Graphite Box for Anode Powder represents a significant step towards sustainable battery production. {company name} has demonstrated its commitment to environmental responsibility and innovation by developing this advanced solution. As the demand for lithium-ion batteries continues to surge, the industry is poised to benefit from the adoption of sustainable manufacturing practices, with the Graphite Box for Anode Powder paving the way for a more sustainable and efficient future.
Micromachined Graphite Rotor Levitated by Diamagnetism for Frictionless Rotation: A Promising Mechanism for Microsensors and Microactuators
Based on Diamagnetic Levitation, Micromachined Graphite Rotor, and Frictionless Microsensors.The development of micromachined graphite rotor based on diamagnetic levitation is a significant breakthrough in the field of microsensors and microactuators. In this research project, a highly oriented pyrolytic graphite (HOPG) rotor is levitated above a permanent magnet structure, allowing for its friction-free rotation.The micropatterned HOPG rotor has four blades with a 1-mm inner diameter disc and a pair of 2-mm outer diameter together with the blades. The levitation height of 132 μm measured for the rotor matches well with a simulation result. The rotor's revolution is demonstrated with the application of gas flow, showing stable continuous actuation with a maximum rate of 500 r/min.The use of a sturdy diamagnetic material, such as HOPG, in micromachined rotors makes them highly valuable for frictionless microsensors. The absence of any friction allows for more precise readings and helps reduce measurement errors. Moreover, the use of diamagnetic levitation technology makes it possible to achieve frictionless motion without the need for complex mechanisms.The promising results of this research project suggest potential applications of the mechanism towards frictionless microsensors and microactuators. The use of micromachined graphite rotors based on diamagnetic levitation can lead to the development of smaller, more efficient, and accurate sensors and actuators.In conclusion, the development of micromachined graphite rotor based on diamagnetic levitation is a significant advancement in the field of microsensors and microactuators. The use of HOPG, a sturdy diamagnetic material, makes it possible to achieve frictionless motion, which can lead to the development of more accurate sensors and actuators. The promising results of this research project suggest potential applications in various industries, including healthcare, aerospace, and robotics.
High-Quality Homemade Graphite Crucible for Various Applications
Homemade Graphite Crucible Revolutionizes the Foundry IndustryIn the world of metal casting, the crucible is an essential component that plays a critical role in the process of melting and pouring metals such as iron, steel, aluminum, and bronze. Traditionally, crucibles were manufactured using clay, silicon carbide, and other refractory materials, but recently, a new player has emerged in the foundry industry – a homemade graphite crucible that is revolutionizing the way metals are cast.The graphite crucible, created by a small, innovative company, has been making waves in the industry due to its unique properties and superior performance. Unlike traditional crucibles, which are often prone to cracking and have limited durability, the homemade graphite crucible offers exceptional thermal stability and resistance to thermal shock. This makes it an ideal choice for foundries looking to improve their casting processes and enhance the quality of their metal products.One of the key advantages of the homemade graphite crucible is its ability to withstand extreme temperatures, making it suitable for use with a wide range of metals and alloys. Its high thermal conductivity allows for rapid and uniform heating, ensuring efficient melting and pouring of metals. Additionally, the graphite material offers excellent chemical inertness, preventing the crucible from reacting with the molten metal and contaminating the final product.Furthermore, the homemade graphite crucible has proven to be highly durable and long-lasting, providing foundries with a cost-effective solution for their casting needs. Unlike traditional crucibles that require frequent replacement due to wear and tear, the graphite crucible can withstand prolonged use without compromising its performance. This not only reduces maintenance and replacement costs but also minimizes downtime, allowing foundries to maximize their productivity and output.In addition to its technical advantages, the homemade graphite crucible is also environmentally friendly. The production process of the crucible involves minimal waste and energy consumption, making it a sustainable option for foundries looking to reduce their environmental footprint. Furthermore, the crucible can be recycled after use, further minimizing its impact on the environment.The company behind the homemade graphite crucible takes pride in its commitment to innovation and quality. With a team of experienced engineers and metallurgists, the company has developed a range of graphite crucibles that are tailored to meet the specific needs of different foundries. Whether it's a small-scale operation or a large industrial foundry, the company offers custom solutions that are designed to maximize performance and efficiency.The success of the homemade graphite crucible has caught the attention of industry leaders and experts, who recognize its potential to transform the foundry industry. In a recent interview, the CEO of a leading foundry remarked, "The homemade graphite crucible has been a game-changer for our operation. It has significantly improved our casting processes, resulting in higher-quality products and increased efficiency."As the demand for high-quality metal products continues to grow, the homemade graphite crucible is poised to play a pivotal role in shaping the future of the foundry industry. Its unique combination of performance, durability, and sustainability has positioned it as a top choice for foundries seeking to stay ahead of the competition.In conclusion, the homemade graphite crucible has emerged as a disruptive force in the foundry industry, offering a new and improved alternative to traditional crucibles. With its superior performance, durability, and environmental benefits, the graphite crucible is set to revolutionize the way metals are cast, paving the way for a more efficient and sustainable future for foundries around the world.
Newly Released Graphite Box Enhances Storage and Transportation of Anode Powder
Graphite Box For Anode Powder Revolutionizes the Battery IndustrySeptember 15, 2022In a groundbreaking move that promises to revolutionize the battery industry, a leading global manufacturer has introduced an innovative product - the Graphite Box for Anode Powder. This cutting-edge solution offers a range of benefits that are set to transform the way batteries are produced, used, and recycled. With its exceptional performance, versatility, and sustainable features, this revolutionary product is set to disrupt the industry status quo.The Graphite Box for Anode Powder is a game-changer when it comes to battery manufacturing. Designed by an industry-leading company known for their commitment to innovation, quality, and sustainability, this ground-breaking product is set to enhance the performance and longevity of batteries across various industries.One of the key advantages of the Graphite Box lies in its exceptional ability to provide stability and consistency in anode powder production. The graphite material is known for its excellent thermal conductivity, which allows for efficient heat dissipation during the battery manufacturing process. This results in superior quality anode powder with optimized electrochemical properties.Furthermore, the Graphite Box boasts outstanding durability, ensuring it can withstand extreme temperature variations and chemical interactions, thereby extending its lifecycle and reducing the frequency of replacements. This not only results in significant cost savings for battery manufacturers but also reduces the environmental impact associated with frequent replacements.To ensure the highest standards of sustainability, the Graphite Box is crafted using eco-friendly materials. By reducing the reliance on non-renewable resources and maximizing energy efficiency, it promotes a greener approach to battery manufacturing. This aligns with the global push towards a more sustainable future and positions the Graphite Box as a frontrunner in supporting environmental conservation efforts.The versatility of the Graphite Box sets it apart from traditional alternatives. It can be used across a wide range of battery types, from lithium-ion batteries in electric vehicles and portable electronics to energy storage systems for renewable sources. This adaptability not only simplifies the manufacturing process but also streamlines the supply chain, making it more efficient and cost-effective.Moreover, the Graphite Box's innovative design allows for easy integration into existing production lines, ensuring a seamless transition for manufacturers. The compatibility and flexibility of this product enable battery manufacturers to optimize their operations without significant disruptions, fostering quicker adoption and industry-wide acceptance.The Graphite Box's impact extends beyond the manufacturing stage. As increasing emphasis is placed on battery recycling to minimize waste, this revolutionary product stands out due to its recyclability. The graphite material is easily separable from other battery components, simplifying the recycling process and minimizing resource wastage. This marks a significant advancement in the circular economy model and reduces the environmental footprint associated with battery disposal.The introduction of the Graphite Box for Anode Powder marks a major milestone in the battery industry, offering unmatched performance, sustainability, and versatility. As the world continues to prioritize renewable energy and electric mobility, this innovative solution presents manufacturers with a powerful tool to meet the surging demand for high-quality, sustainable batteries. With its potential to reduce costs, improve battery performance, and contribute to a cleaner planet, the Graphite Box is set to reshape the industry landscape and unlock a new era of battery technology.About the Company:The company behind the Graphite Box for Anode Powder is a global leader in advanced materials and technology solutions for various industries. With a strong focus on research and development, innovation, and sustainability, they are dedicated to delivering cutting-edge products that surpass customer expectations. With a robust global presence and an unwavering commitment to quality, this company continues to shape the future of industries around the world.
Small Bronze Casting Electric Foundry - Techniques for Smelting and Melting Metal
Electric Foundry for Small Bronze CastingFor aspiring artisans and small-scale metalworkers, the ability to create intricate shapes and designs through the lost wax casting process is essential. And while traditional molding techniques are can deliver beautiful results, obtaining the necessary equipment such as a reliable foundry can be quite challenging especially for hobbyists. Fortunately, with modern technology, it is now easier than ever to acquire capable tools that make it possible to melt metals at home, even in small quantities. This article will introduce you to the concept of an electric foundry for small bronze casting, and discuss its features and benefits as well as limitations.Background Information: The Smelting and Casting ProcessSmelting is the process of melting metal from its natural state, while casting refers to the process of using molds to create shapes and forms that would be impossible with traditional tools. The combination of these processes is referred to as foundry work, while the furnace used to achieve these processes is often referred to as a foundry. Historically, foundries were large, fiery beasts that required extensive knowledge to operate and were often housed in large, industrial type buildings. However, the advent of electric foundries made the process more accessible to the common person, allowing small artisans to cast their own designs in small quantities, for commercial or personal use.Features of an Electric FoundryAn electric foundry is a metalworking tool used primarily for melting various metals such as bronze, silver, and gold. It is powered by electricity, typically 240 V or 110 V, and operates through electric heating coils, which generate heat by an electric current passing through them. Whereas conventional foundries may use gas or oil as their heat source to melt metals, electric foundries are powered by electricity, which makes them highly efficient, clean and energy-efficient.Electric foundries are available in different configurations and sizes, with varying power ratings. The size of the foundry will directly affect the amount of metal that can be melted, as well as the level of heat capacity, or the amount of heat required to melt the metal. For homeowners and hobbyists, a small electric foundry may suffice, often fitted with a single heating coil, whereas larger foundries may have multiple heating coils, allowing for higher temperature readings and capacity.The Benefits of Using an Electric FoundryElectric foundries come with plenty of perks, which make them a go-to choice for homeowners and hobbyists. Here are some benefits of using an electric foundry:Precision Temperature Control: An electric foundry comes with precise temperature controls that enable you to maintain a stable and consistent temperature for your desired metal. This means even the most delicate metals can be melted using electric foundries. The stable temperature control also means there is less risk of accidental overheating.Energy-Efficient: Electric foundries tend to consume more energy upfront but are energy-efficient in the long run. Compared to gas or oil-based foundries that rely on nonrenewable resources, electric foundries do not produce waste byproducts, and require minimal upkeep once installed.Cost-Effective: Electric foundries are generally more affordable to operate than traditional combustion-based foundries. This is mainly because their heating mechanisms use electricity, which is readily available and low-cost.Reduced Emissions: Electric foundries do not produce emissions, making them an environmentally friendly option.Limitations of Using an Electric FoundryDespite their obvious advantages, electric foundries come with some downsides. Here are a few:Limited Capacity: Electric foundries are often limited in their melting capacity, meaning you may need to melt multiple batches of metal to achieve the desired outcome.Power Constraints: Depending on the size and power of the electric foundry being used, it may require a lot of power to operate. This may require some modifications to your household's electrical systems depending on your voltage level and the foundry's output.ConclusionAn electric foundry is an ideal solution for melting small amounts of metals like bronze, gold, or silver efficiently and with minimal fuss. Its precise temperature controls and energy efficiency make it an excellent choice for small-scale metalworkers, from hobbyists looking to practice lost wax casting to jewelers crafting intricate designs for customers. While it has limitations when compared to traditional combustion-based foundries, it remains a great option for a cost-effective and environmentally friendly way of melting metals. With the proper setup and safety measures, using an electric foundry for small-scale metalworking may be your ticket to creating beautiful works of art from the comfort of your home.